Order Now
- Home
- About Us
-
Services
-
Assignment Writing
-
Academic Writing Services
- HND Assignment Help
- SPSS Assignment Help
- College Assignment Help
- Writing Assignment for University
- Urgent Assignment Help
- Architecture Assignment Help
- Total Assignment Help
- All Assignment Help
- My Assignment Help
- Student Assignment Help
- Instant Assignment Help
- Cheap Assignment Help
- Global Assignment Help
- Write My Assignment
- Do My Assignment
- Solve My Assignment
- Make My Assignment
- Pay for Assignment Help
-
Management
- Management Assignment Help
- Business Management Assignment Help
- Financial Management Assignment Help
- Project Management Assignment Help
- Supply Chain Management Assignment Help
- Operations Management Assignment Help
- Risk Management Assignment Help
- Strategic Management Assignment Help
- Logistics Management Assignment Help
- Global Business Strategy Assignment Help
- Consumer Behavior Assignment Help
- MBA Assignment Help
- Portfolio Management Assignment Help
- Change Management Assignment Help
- Hospitality Management Assignment Help
- Healthcare Management Assignment Help
- Investment Management Assignment Help
- Market Analysis Assignment Help
- Corporate Strategy Assignment Help
- Conflict Management Assignment Help
- Marketing Management Assignment Help
- Strategic Marketing Assignment Help
- CRM Assignment Help
- Marketing Research Assignment Help
- Human Resource Assignment Help
- Business Assignment Help
- Business Development Assignment Help
- Business Statistics Assignment Help
- Business Ethics Assignment Help
- 4p of Marketing Assignment Help
- Pricing Strategy Assignment Help
- Nursing
-
Finance
- Finance Assignment Help
- Do My Finance Assignment For Me
- Financial Accounting Assignment Help
- Behavioral Finance Assignment Help
- Finance Planning Assignment Help
- Personal Finance Assignment Help
- Financial Services Assignment Help
- Forex Assignment Help
- Financial Statement Analysis Assignment Help
- Capital Budgeting Assignment Help
- Financial Reporting Assignment Help
- International Finance Assignment Help
- Business Finance Assignment Help
- Corporate Finance Assignment Help
-
Accounting
- Accounting Assignment Help
- Managerial Accounting Assignment Help
- Taxation Accounting Assignment Help
- Perdisco Assignment Help
- Solve My Accounting Paper
- Business Accounting Assignment Help
- Cost Accounting Assignment Help
- Taxation Assignment Help
- Activity Based Accounting Assignment Help
- Tax Accounting Assignment Help
- Financial Accounting Theory Assignment Help
-
Computer Science and IT
- Operating System Assignment Help
- Data mining Assignment Help
- Robotics Assignment Help
- Computer Network Assignment Help
- Database Assignment Help
- IT Management Assignment Help
- Network Topology Assignment Help
- Data Structure Assignment Help
- Business Intelligence Assignment Help
- Data Flow Diagram Assignment Help
- UML Diagram Assignment Help
- R Studio Assignment Help
-
Law
- Law Assignment Help
- Business Law Assignment Help
- Contract Law Assignment Help
- Tort Law Assignment Help
- Social Media Law Assignment Help
- Criminal Law Assignment Help
- Employment Law Assignment Help
- Taxation Law Assignment Help
- Commercial Law Assignment Help
- Constitutional Law Assignment Help
- Corporate Governance Law Assignment Help
- Environmental Law Assignment Help
- Criminology Assignment Help
- Company Law Assignment Help
- Human Rights Law Assignment Help
- Evidence Law Assignment Help
- Administrative Law Assignment Help
- Enterprise Law Assignment Help
- Migration Law Assignment Help
- Communication Law Assignment Help
- Law and Ethics Assignment Help
- Consumer Law Assignment Help
- Science
- Biology
- Engineering
-
Humanities
- Humanities Assignment Help
- Sociology Assignment Help
- Philosophy Assignment Help
- English Assignment Help
- Geography Assignment Help
- Agroecology Assignment Help
- Psychology Assignment Help
- Social Science Assignment Help
- Public Relations Assignment Help
- Political Science Assignment Help
- Mass Communication Assignment Help
- History Assignment Help
- Cookery Assignment Help
- Auditing
- Mathematics
-
Economics
- Economics Assignment Help
- Managerial Economics Assignment Help
- Econometrics Assignment Help
- Microeconomics Assignment Help
- Business Economics Assignment Help
- Marketing Plan Assignment Help
- Demand Supply Assignment Help
- Comparative Analysis Assignment Help
- Health Economics Assignment Help
- Macroeconomics Assignment Help
- Political Economics Assignment Help
- International Economics Assignments Help
-
Academic Writing Services
-
Essay Writing
- Essay Help
- Essay Writing Help
- Essay Help Online
- Online Custom Essay Help
- Descriptive Essay Help
- Help With MBA Essays
- Essay Writing Service
- Essay Writer For Australia
- Essay Outline Help
- illustration Essay Help
- Response Essay Writing Help
- Professional Essay Writers
- Custom Essay Help
- English Essay Writing Help
- Essay Homework Help
- Literature Essay Help
- Scholarship Essay Help
- Research Essay Help
- History Essay Help
- MBA Essay Help
- Plagiarism Free Essays
- Writing Essay Papers
- Write My Essay Help
- Need Help Writing Essay
- Help Writing Scholarship Essay
- Help Writing a Narrative Essay
- Best Essay Writing Service Canada
-
Dissertation
- Biology Dissertation Help
- Academic Dissertation Help
- Nursing Dissertation Help
- Dissertation Help Online
- MATLAB Dissertation Help
- Doctoral Dissertation Help
- Geography Dissertation Help
- Architecture Dissertation Help
- Statistics Dissertation Help
- Sociology Dissertation Help
- English Dissertation Help
- Law Dissertation Help
- Dissertation Proofreading Services
- Cheap Dissertation Help
- Dissertation Writing Help
- Marketing Dissertation Help
- Programming
-
Case Study
- Write Case Study For Me
- Business Law Case Study Help
- Civil Law Case Study Help
- Marketing Case Study Help
- Nursing Case Study Help
- Case Study Writing Services
- History Case Study help
- Amazon Case Study Help
- Apple Case Study Help
- Case Study Assignment Help
- ZARA Case Study Assignment Help
- IKEA Case Study Assignment Help
- Zappos Case Study Assignment Help
- Tesla Case Study Assignment Help
- Flipkart Case Study Assignment Help
- Contract Law Case Study Assignments Help
- Business Ethics Case Study Assignment Help
- Nike SWOT Analysis Case Study Assignment Help
- Coursework
- Thesis Writing
- CDR
- Research
-
Assignment Writing
-
Resources
- Referencing Guidelines
-
Universities
-
Australia
- Asia Pacific International College Assignment Help
- Macquarie University Assignment Help
- Rhodes College Assignment Help
- APIC University Assignment Help
- Torrens University Assignment Help
- Kaplan University Assignment Help
- Holmes University Assignment Help
- Griffith University Assignment Help
- VIT University Assignment Help
- CQ University Assignment Help
-
Australia
- Experts
- Free Sample
- Testimonial
MME501 Materials of Engineers Report 3 Sample
Task 1:
Case Study on Materials Used in Modern Aircraft:
Carefully read the below text and answer the following questions.
It is strongly suggested to refer to the lecture notes, recommended textbooks, and other literature in formulating your answers. It is not necessary to use question numbers, but make sure to provide sufficient explanations to cover the questions.
You may use figures, diagrams and tables to illustrate your answer and provide citations and references, where necessary.
The answer should contain a minimum of 500 words.
“Composite materials have been called the shape of aerospace’s future. With their winning combination of high strength, low weight and durability, it’s easy to see why. For more than 30 years, Airbus has pioneered the use of such materials in its commercial jetliners, from the cornerstone A310’s vertical stabiliser to today’s A350 XWB – on which more than half of the aircraft’s structure is composite.
In essence, a composite material is made from two or more constituent materials with different physical or chemical properties. When combined, the composite material exhibits beneficial physical characteristics quite different from what the individual components alone can provide. Commonly- recognised composites in everyday life include plywood and reinforced concrete.
From nose to tail, Airbus utilizes advanced composites in its jetliner product line that have been at the forefront of materials science. One particular standout material is carbon-fibre reinforced plastic, or CFRP. Composed of carbon fibres locked into place with a plastic resin, CFRP offers a better strength-to-weight ratio than metals and has less sensitivity to fatigue and corrosion. In short, it’s lighter than aluminium, stronger than iron, and more corrosion-resistant than both.
Like all composites, the strength of CFRP results from the interplay between its component materials. By themselves, neither the carbon fibres nor the resin is sufficient to create a product with the desired characteristics to be integrated on an aircraft. But once combined in multiple, integrated layers and bonded, the CFRP airframe component or aerostructure takes on the strength and load- bearing properties that make it ideal for aviation use.”
(Source: https://www.airbus.com)
Discuss advantages of using non-metals in aircraft structures.
Investigate the extent of usage of non-metals in A350 aircraft or a similar aircraft.
Compare the use of CFRP in A350 aircraft with traditional materials used for older versions of aircraft. It is required to compare strength, durability and other key properties and quote suitable examples of components for which these different materials are used.
Investigate the limitations of using non-metals in aircraft structures.
Task 2:
“Strain hardening is the phenomenon whereby a ductile metal becomes harder and stronger as it is plastically deformed. Sometimes it is also called work hardening, or, because the temperature at which deformation takes place is “cold” relative to the absolute melting temperature of the metal, cold working. Most metals strain harden at room temperature” – Materials Science and Engineering, Callister, 8th Edition
The figure on the left below demonstrates how steel, brass, and copper increase tensile strength with increasing the degree of cold work. The price for this enhancement of strength is in the ductility of the metal. The reduction in ductility with the percentage of cold work is shown in the figure on the right.
Source: Materials Science and Engineering, Callister, 8th Edition
Once a cold worked material is heat treated, the recrystallization process resets the cold work properties to zero cold work case. Therefore, when excessive cold work is required without sacrificing the ductility of a material, a component is partially cold worked which is followed by heat treatment to reset the properties before the next stage of cold work. This process may be repeated for number of times as required.
Use the above explanation and the graphs to answer the following questions.
A cylindrical rod of brass originally 10.2 mm in diameter is to be cold worked by drawing. The circular cross section will be maintained during deformation. A cold-worked tensile strength in excess of 380 MPa and a ductility of at least 15 %EL are desired. Furthermore, the final diameter must be 7.6 mm.
Hint: The following process may be followed to achieve the requirement.
Calculate the percentage cold work expected during the drawing which reduces the diameter from 10.2 mm to 7.6 mm. Use the given diagrams to justify that the required tensile strength and/or the ductility cannot be matched with the proposed amount of cold work.
As an alternative, consider the required values of tensile strength and the ductility, separately to determine the target values of percentage of cold work and hence propose a suitable range for the percentage of cold work. Considering the range, decide on a suitable amount of cold work.
It is suggested that to reduce the diameter of the rod to an intermediate value to satisfy the proposed percentage of cold work in b) above. Apply the cold work formula to determine the final diameter of the rod after this first stage of the cold work.
Explain the rest of the process of reducing the cross section to 7.6 mm diameter whilst achieving the required ductility and tensile strength. What is the percentage of cold work retained in the rod?
Task 3: (30 marks)
3.1
It is required to select suitable material/s for an engineering application that satisfies the following requirements:
Tensile strength more than 700 MPa
Modulus of elasticity more than 100 GPa
Density less than 3000 kg/m3
3.2
Answer following questions.
Use the first two Ashby charts (below) to select a set of materials that satisfy these requirements.
Use the third Ashby chart, standard textbooks and/or any other resource/s to refine your selection to present three best materials if the following additional requirements are also to be fulfilled.
Corrosion resistance
Low cost
Sustainability
Explain the selection process in each case quoting any references used.
Solution
Task 1 (a)
In contrast to conventional metals, the use of non-metallic materials, particularly composites, offers a number of benefits. Here are a few of the main advantages:
1. Excellent strength to weight ratio: Composites outperform conventional metals in this regard. For instance, aluminium is substantially heavier than carbon fibre reinforced plastic (CFRP), a prominent composite material used in aerospace applications, but it has comparable or even higher strength.
2. Durability: In difficult situations, composites are also more durable than conventional metals. They are perfect for aviation constructions that must withstand harsh circumstances since they are less sensitive to fatigue and corrosion.
3. Design Adaptability: Composites may be shaped into intricate forms, increasing design adaptability and maximising material usage. Reduced weight and improved fuel economy are the outcomes, which are crucial for commercial aircraft.
4. Lower Maintenance Costs: Due to their longevity, composites need less maintenance than conventional metals. Over the course of an aircraft, this can save a lot of money.
5. Better Performance: Using composite materials in aircraft constructions can lead to better performance, especially in terms of speed, range, and cargo capacity. This is due to the fact that composites have a greater strength-to-weight ratio, which leads to improved efficiency and performance.
Task 1 (b)
Modern commercial aircraft like the Airbus A350 XWB (Extra Wide Body) heavily rely on non-metallic components, notably composites. In reality, composite materials, including carbon-fibre reinforced plastic (CFRP) and other cutting-edge materials, make up more than half of the aircraft's construction. Here are some instances of how the A350 uses composite materials:
1. The A350's wings are predominantly constructed of CFRP, which is stronger and lighter than aluminium. By stacking pre-impregnated carbon fibre material in a mould and then curing it at high temperatures to form a solid, one-piece structure, a novel manufacturing technique is used to manufacture the wings.
2. Fuselage: Materials like as CFRP and other composites are used to construct the A350's fuselage. Similar stacking and curing techniques are used to create the fuselage to generate a sturdy, light-weight structure that is corrosion- and fatigue-resistant.
3. The A350's horizontal tail plane and vertical stabiliser are likewise composed of composite materials, including CFRP. To build a sturdy, lightweight framework, these components are made utilising a combination of manual lay-up and automated lay-up procedures.
4. Landing Gear Doors: GLARE (Glass Laminate Aluminium Reinforced Epoxy), a composite material, is used to construct the landing gear doors of the A350. The hybrid material GLARE is made of layers of fibreglass and aluminium, creating a robust, light-weight framework that is resistant to fatigue and corrosion.
Task 1 (c)
The A350 aircraft's usage of CFRP marks a substantial change from the conventional materials used in earlier models of aircraft. Some of the main variations between the two are as follows:
Strength: Compared to conventional materials like aluminium or steel, CFRP offers a better strength-to-weight ratio. For instance, the wing of the A350 XWB is entirely composed of CFRP, which results in a weight savings of 25% when compared to a traditional metal wing of comparable size. Lower running costs and improved fuel economy are the consequences.
Durability: Compared to conventional metals, CFRP is less prone to corrosion and fatigue. For instance, the 53% CFRP fuselage of the A350 XWB makes it more corrosive resistant and less prone to fatigue fractures. Longer service life and lower maintenance expenses result from this.
Component examples: In addition to the wing and fuselage, the A350 XWB also heavily utilises CFRP in the tail section, nose cone, and doors.
Task 1 (d)
There are several advantages for The Assignment help to using non-metals, notably composites, in aeroplane construction, as the text emphasises. There are several restrictions to take into account, though:
1. Price: Producing composite materials may be expensive and necessitates specialised production techniques. The materials themselves may be more expensive than conventional metals, and the initial investment in production-related tools and training may be high.
2. Maintenance: Compared to typical metal constructions, composite structures may require more effort and time to fix. It may be necessary to purchase specialised tools and training, which will raise the overall cost of maintenance.
3. Robustness: Despite being more resilient than metals in general, composites might be more vulnerable to damage from external elements including UV light, dampness, and severe temperatures.
4. Fire resistance: Composite materials can be less fire-resistant than metals, and may require additional fireproofing measures to meet safety regulations.
Top of Form
Task 2 (a)
To calculate the percentage cold work, we can use the formula:
According to the figure on the left, brass's tensile strength improves as the amount of cold work increases; a cold-worked tensile strength of more than 380 MPa may be attained with a cold work of around 50%. The figure to the right shows, however, that brass's ductility rapidly declines as the amount of cold work increases, and a ductility of at least 15%EL cannot be obtained with a cold work of 50%. Because of this, the suggested level of cold work (44.3%) is insufficient to provide the appropriate levels of tensile strength and ductility.
Task 2 (b)
Looking at the figure on the left, we can see that a cold work of roughly 50% is necessary for brass in order to attain the appropriate tensile strength of 380 MPa. But as we can see from the figure on the right, a 50% cold work yields a ductility of less than 10%EL. Looking at the figure to the right, we can see that a cold work of less than 30% is necessary for brass in order to reach the needed ductility of at least 15%EL. But as we can see from the figure on the left, a 30% cold work yields a tensile strength of about 280 MPa, which is significantly less than the desired 380 MPa.
To attain the appropriate tensile strength and ductility, we must thus choose an acceptable range of cold work. The data show that a tensile strength of around 400 MPa and a ductility of about 12%EL may be obtained from a cold work of about 40%. In light of this, 35–45% of cold labour would be appropriate in this situation. We may select a 40% cold work, which is towards the middle of the range and should produce tensile strength of about 400 MPa and ductility of about 12%EL.
Top of Form
Task 2 (c)
To achieve a cold work of 40%, it is suggested to perform the cold work in multiple stages. Let's assume that the initial diameter of the rod is reduced to an intermediate value (D_i) such that the final diameter after the second stage of cold work is 7.6 mm.
From the formula for percentage cold work, we can write:
Therefore, the diameter of the rod should be reduced to 8.76 mm in the first stage of cold work, and then further reduced to 7.6 mm in the second stage of cold work to achieve a total cold work of 40%.
Task 2 (d)
To achieve a final diameter of 7.6 mm with a total cold work of 40%, the rod needs to be cold worked in two stages:
First stage: Reduce the diameter from 10.2 mm to 8.76 mm. This corresponds to a cold work of 14.1%.
Second stage: Reduce the diameter from 8.76 mm to 7.6 mm. This corresponds to a cold work of 26.1%.
After the first stage of cold work, the material should be heat treated to reset the cold work properties before the second stage of cold work. This is important to avoid excessive hardening and embrittlement of the material.
Assuming that the heat treatment successfully reset the cold work properties after the first stage, the total percentage of cold work in the final product will be:
Therefore, the percentage of cold work retained in the rod after the second stage of cold work is 40.2%. Since this value is close to the target range of 35-45% calculated in part (b), we can expect the final product to have a tensile strength of about 400 MPa and a ductility of about 12%EL, as discussed earlier.
Task 3
It is required to select suitable material/s for an engineering application that satisfies the following requirements:
Tensile strength more than 700 MPa
Modulus of elasticity more than 100 GPa
Density less than 3000 kg/m3
Task 3 (a)
To satisfy the given requirements, we need to find materials with a high tensile strength and modulus of elasticity, while also having a low density. We can start by looking at materials with high tensile strength and modulus of elasticity from the first Ashby chart.
Materials such as titanium alloys, high-strength steels, and some aluminum alloys have high tensile strength and modulus of elasticity. However, these materials are generally dense and may not meet the density requirement.
To meet the density requirement, we need to look at materials with a low density from the second Ashby chart, such as carbon fiber composites or polymer-based materials. However, these materials typically have a lower tensile strength and modulus of elasticity compared to metals.
Therefore, we need to strike a balance between these requirements by selecting a material that offers a good compromise between strength, stiffness, and density. One such material that meets these requirements is carbon fiber reinforced polymer (CFRP). CFRP has a tensile strength of around 700-1400 MPa, a modulus of elasticity of 100-300 GPa, and a density of around 1600-1900 kg/m^3. Other composite materials such as fiberglass or Kevlar may also be suitable depending on the specific requirements of the engineering application.
Task 3 (b)
To refine our selection of materials, we will consider the additional requirements of corrosion resistance, low cost, and sustainability. We will use the Ashby chart on strength versus relative cost per unit volume, along with standard textbooks and other resources, to select the three best materials.
Corrosion Resistance: For many engineering applications, especially those that involve exposure to hostile conditions like marine or aircraft settings, corrosion resistance is a crucial requirement. We will use the Ashby corrosion resistance vs strength table to choose materials that satisfy this criteria. Materials with strong corrosion resistance, high tensile strength, and elastic modulus include titanium, aluminium alloys, and stainless steel. However, they might not be affordable enough.
However, despite being less expensive, materials like polymers and composites might not provide the necessary level of corrosion resistance.
A fiber-reinforced polymer composite that employs an epoxy matrix and carbon or glass fibres is one substance that satisfies all three criteria. This substance offers excellent corrosion resistance, great strength and stiffness, and low density. In comparison to materials like titanium and stainless steel, it is also very inexpensive.
Low Cost: For numerous engineering uses, especially those requiring mass production or large-scale building, low cost is a crucial need. We will use the Ashby table on relative cost per unit volume vs strength to choose materials that satisfy this criterion.
Although materials like polymers and composites are typically less expensive than metals, they might not provide the necessary level of strength and stiffness. Although more expensive, metals like steel and aluminium alloys have higher strength and stiffness.
One substance that satisfies all three demands is aluminium 7075 alloy. This alloy has a comparatively low density of near 2800 kg/m3, a high tensile strength of about 600 MPa, and an elastic modulus of about 70 GPa. Moreover, it is relatively low in cost compared to other high-strength metals such as titanium.
Sustainability: As businesses and organisations work to lessen their environmental effect, sustainability is becoming a criterion for engineering applications that must be met. We shall take into account aspects including recyclability, energy usage during manufacture, and the environmental effect of the material's life cycle when choosing materials to satisfy this criterion. Materials like metals and alloys take a lot of energy to manufacture, and this process frequently pollutes the environment. On the other hand, recyclable materials with a lesser environmental effect include composites and polymers.
Composite made of bamboo fibres and reinforced with polymer is one material that satisfies all three criteria. Compared to other materials like metals and synthetic polymers, bamboo is a more environmentally friendly resource since it is very sustainable and regenerative. A range of technical applications can benefit from the strength and rigidity of bamboo fiber-reinforced polymer composites.
Finally, we have chosen three materials that satisfy the initial specifications of high tensile strength, elastic modulus, and low density. We then used Ashby tables and other resources to narrow down our pick based on the additional criteria of corrosion resistance, affordability, and sustainability. A fiber-reinforced polymer composite, aluminium 7075 alloy, and a composite made of bamboo fibres were chosen as the materials. These materials are useful for a variety of technical applications because they provide a reasonable balance between strength, stiffness, and other criteria.
Reference
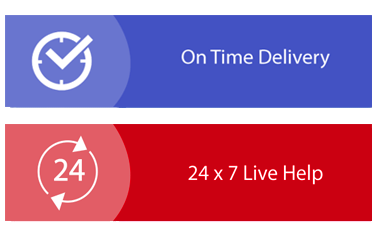
Download Samples PDF
Related Sample
- MGMT20143 Idea Generation and Business Model Development Assignment
- BDA601 Big Data and Analytics Report
- Auditing Coursework Assignment
- SENG205 Software Engineering Assignment
- LAW5398 Construction Law Assignment
- BUS5PB Principles of Business Analytics Assignment
- MCR007 Introduction To Project Management Assignment
- MG401 Leadership in Agribusiness Part c Report 2
- PSYC1003 Understanding Mind Brain and Behaviour Assignment
- BUGEN5930 Business Society and The Planet Assignment
- MIS101 Information Systems for Business Assignment
- Technology and Engineering Management Assignment
- MATH11247 Foundation Mathematics Assignment 2
- Managing Information Systems Technology Projects
- BE553 Principles of International Marketing Assignment
- An Essay on Accounts Receivable Assignment
- EVN301 Events Policy and Strategy Assignment
- MBA600 Capstone Strategy Essay
- CPCCOM1013 Plan and Organize Work
- MITS4001 Business Information System Assignment
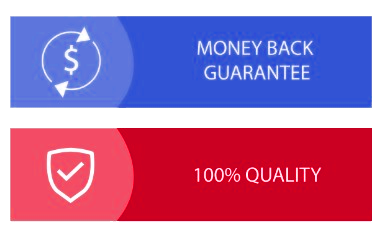
Assignment Services
-
Assignment Writing
-
Academic Writing Services
- HND Assignment Help
- SPSS Assignment Help
- College Assignment Help
- Writing Assignment for University
- Urgent Assignment Help
- Architecture Assignment Help
- Total Assignment Help
- All Assignment Help
- My Assignment Help
- Student Assignment Help
- Instant Assignment Help
- Cheap Assignment Help
- Global Assignment Help
- Write My Assignment
- Do My Assignment
- Solve My Assignment
- Make My Assignment
- Pay for Assignment Help
-
Management
- Management Assignment Help
- Business Management Assignment Help
- Financial Management Assignment Help
- Project Management Assignment Help
- Supply Chain Management Assignment Help
- Operations Management Assignment Help
- Risk Management Assignment Help
- Strategic Management Assignment Help
- Logistics Management Assignment Help
- Global Business Strategy Assignment Help
- Consumer Behavior Assignment Help
- MBA Assignment Help
- Portfolio Management Assignment Help
- Change Management Assignment Help
- Hospitality Management Assignment Help
- Healthcare Management Assignment Help
- Investment Management Assignment Help
- Market Analysis Assignment Help
- Corporate Strategy Assignment Help
- Conflict Management Assignment Help
- Marketing Management Assignment Help
- Strategic Marketing Assignment Help
- CRM Assignment Help
- Marketing Research Assignment Help
- Human Resource Assignment Help
- Business Assignment Help
- Business Development Assignment Help
- Business Statistics Assignment Help
- Business Ethics Assignment Help
- 4p of Marketing Assignment Help
- Pricing Strategy Assignment Help
- Nursing
-
Finance
- Finance Assignment Help
- Do My Finance Assignment For Me
- Financial Accounting Assignment Help
- Behavioral Finance Assignment Help
- Finance Planning Assignment Help
- Personal Finance Assignment Help
- Financial Services Assignment Help
- Forex Assignment Help
- Financial Statement Analysis Assignment Help
- Capital Budgeting Assignment Help
- Financial Reporting Assignment Help
- International Finance Assignment Help
- Business Finance Assignment Help
- Corporate Finance Assignment Help
-
Accounting
- Accounting Assignment Help
- Managerial Accounting Assignment Help
- Taxation Accounting Assignment Help
- Perdisco Assignment Help
- Solve My Accounting Paper
- Business Accounting Assignment Help
- Cost Accounting Assignment Help
- Taxation Assignment Help
- Activity Based Accounting Assignment Help
- Tax Accounting Assignment Help
- Financial Accounting Theory Assignment Help
-
Computer Science and IT
- Operating System Assignment Help
- Data mining Assignment Help
- Robotics Assignment Help
- Computer Network Assignment Help
- Database Assignment Help
- IT Management Assignment Help
- Network Topology Assignment Help
- Data Structure Assignment Help
- Business Intelligence Assignment Help
- Data Flow Diagram Assignment Help
- UML Diagram Assignment Help
- R Studio Assignment Help
-
Law
- Law Assignment Help
- Business Law Assignment Help
- Contract Law Assignment Help
- Tort Law Assignment Help
- Social Media Law Assignment Help
- Criminal Law Assignment Help
- Employment Law Assignment Help
- Taxation Law Assignment Help
- Commercial Law Assignment Help
- Constitutional Law Assignment Help
- Corporate Governance Law Assignment Help
- Environmental Law Assignment Help
- Criminology Assignment Help
- Company Law Assignment Help
- Human Rights Law Assignment Help
- Evidence Law Assignment Help
- Administrative Law Assignment Help
- Enterprise Law Assignment Help
- Migration Law Assignment Help
- Communication Law Assignment Help
- Law and Ethics Assignment Help
- Consumer Law Assignment Help
- Science
- Biology
- Engineering
-
Humanities
- Humanities Assignment Help
- Sociology Assignment Help
- Philosophy Assignment Help
- English Assignment Help
- Geography Assignment Help
- Agroecology Assignment Help
- Psychology Assignment Help
- Social Science Assignment Help
- Public Relations Assignment Help
- Political Science Assignment Help
- Mass Communication Assignment Help
- History Assignment Help
- Cookery Assignment Help
- Auditing
- Mathematics
-
Economics
- Economics Assignment Help
- Managerial Economics Assignment Help
- Econometrics Assignment Help
- Microeconomics Assignment Help
- Business Economics Assignment Help
- Marketing Plan Assignment Help
- Demand Supply Assignment Help
- Comparative Analysis Assignment Help
- Health Economics Assignment Help
- Macroeconomics Assignment Help
- Political Economics Assignment Help
- International Economics Assignments Help
-
Academic Writing Services
-
Essay Writing
- Essay Help
- Essay Writing Help
- Essay Help Online
- Online Custom Essay Help
- Descriptive Essay Help
- Help With MBA Essays
- Essay Writing Service
- Essay Writer For Australia
- Essay Outline Help
- illustration Essay Help
- Response Essay Writing Help
- Professional Essay Writers
- Custom Essay Help
- English Essay Writing Help
- Essay Homework Help
- Literature Essay Help
- Scholarship Essay Help
- Research Essay Help
- History Essay Help
- MBA Essay Help
- Plagiarism Free Essays
- Writing Essay Papers
- Write My Essay Help
- Need Help Writing Essay
- Help Writing Scholarship Essay
- Help Writing a Narrative Essay
- Best Essay Writing Service Canada
-
Dissertation
- Biology Dissertation Help
- Academic Dissertation Help
- Nursing Dissertation Help
- Dissertation Help Online
- MATLAB Dissertation Help
- Doctoral Dissertation Help
- Geography Dissertation Help
- Architecture Dissertation Help
- Statistics Dissertation Help
- Sociology Dissertation Help
- English Dissertation Help
- Law Dissertation Help
- Dissertation Proofreading Services
- Cheap Dissertation Help
- Dissertation Writing Help
- Marketing Dissertation Help
- Programming
-
Case Study
- Write Case Study For Me
- Business Law Case Study Help
- Civil Law Case Study Help
- Marketing Case Study Help
- Nursing Case Study Help
- Case Study Writing Services
- History Case Study help
- Amazon Case Study Help
- Apple Case Study Help
- Case Study Assignment Help
- ZARA Case Study Assignment Help
- IKEA Case Study Assignment Help
- Zappos Case Study Assignment Help
- Tesla Case Study Assignment Help
- Flipkart Case Study Assignment Help
- Contract Law Case Study Assignments Help
- Business Ethics Case Study Assignment Help
- Nike SWOT Analysis Case Study Assignment Help
- Coursework
- Thesis Writing
- CDR
- Research