Order Now
- Home
- About Us
-
Services
-
Assignment Writing
-
Academic Writing Services
- HND Assignment Help
- SPSS Assignment Help
- College Assignment Help
- Writing Assignment for University
- Urgent Assignment Help
- Architecture Assignment Help
- Total Assignment Help
- All Assignment Help
- My Assignment Help
- Student Assignment Help
- Instant Assignment Help
- Cheap Assignment Help
- Global Assignment Help
- Write My Assignment
- Do My Assignment
- Solve My Assignment
- Make My Assignment
- Pay for Assignment Help
-
Management
- Management Assignment Help
- Business Management Assignment Help
- Financial Management Assignment Help
- Project Management Assignment Help
- Supply Chain Management Assignment Help
- Operations Management Assignment Help
- Risk Management Assignment Help
- Strategic Management Assignment Help
- Logistics Management Assignment Help
- Global Business Strategy Assignment Help
- Consumer Behavior Assignment Help
- MBA Assignment Help
- Portfolio Management Assignment Help
- Change Management Assignment Help
- Hospitality Management Assignment Help
- Healthcare Management Assignment Help
- Investment Management Assignment Help
- Market Analysis Assignment Help
- Corporate Strategy Assignment Help
- Conflict Management Assignment Help
- Marketing Management Assignment Help
- Strategic Marketing Assignment Help
- CRM Assignment Help
- Marketing Research Assignment Help
- Human Resource Assignment Help
- Business Assignment Help
- Business Development Assignment Help
- Business Statistics Assignment Help
- Business Ethics Assignment Help
- 4p of Marketing Assignment Help
- Pricing Strategy Assignment Help
- Nursing
-
Finance
- Finance Assignment Help
- Do My Finance Assignment For Me
- Financial Accounting Assignment Help
- Behavioral Finance Assignment Help
- Finance Planning Assignment Help
- Personal Finance Assignment Help
- Financial Services Assignment Help
- Forex Assignment Help
- Financial Statement Analysis Assignment Help
- Capital Budgeting Assignment Help
- Financial Reporting Assignment Help
- International Finance Assignment Help
- Business Finance Assignment Help
- Corporate Finance Assignment Help
-
Accounting
- Accounting Assignment Help
- Managerial Accounting Assignment Help
- Taxation Accounting Assignment Help
- Perdisco Assignment Help
- Solve My Accounting Paper
- Business Accounting Assignment Help
- Cost Accounting Assignment Help
- Taxation Assignment Help
- Activity Based Accounting Assignment Help
- Tax Accounting Assignment Help
- Financial Accounting Theory Assignment Help
-
Computer Science and IT
- Operating System Assignment Help
- Data mining Assignment Help
- Robotics Assignment Help
- Computer Network Assignment Help
- Database Assignment Help
- IT Management Assignment Help
- Network Topology Assignment Help
- Data Structure Assignment Help
- Business Intelligence Assignment Help
- Data Flow Diagram Assignment Help
- UML Diagram Assignment Help
- R Studio Assignment Help
-
Law
- Law Assignment Help
- Business Law Assignment Help
- Contract Law Assignment Help
- Tort Law Assignment Help
- Social Media Law Assignment Help
- Criminal Law Assignment Help
- Employment Law Assignment Help
- Taxation Law Assignment Help
- Commercial Law Assignment Help
- Constitutional Law Assignment Help
- Corporate Governance Law Assignment Help
- Environmental Law Assignment Help
- Criminology Assignment Help
- Company Law Assignment Help
- Human Rights Law Assignment Help
- Evidence Law Assignment Help
- Administrative Law Assignment Help
- Enterprise Law Assignment Help
- Migration Law Assignment Help
- Communication Law Assignment Help
- Law and Ethics Assignment Help
- Consumer Law Assignment Help
- Science
- Biology
- Engineering
-
Humanities
- Humanities Assignment Help
- Sociology Assignment Help
- Philosophy Assignment Help
- English Assignment Help
- Geography Assignment Help
- Agroecology Assignment Help
- Psychology Assignment Help
- Social Science Assignment Help
- Public Relations Assignment Help
- Political Science Assignment Help
- Mass Communication Assignment Help
- History Assignment Help
- Cookery Assignment Help
- Auditing
- Mathematics
-
Economics
- Economics Assignment Help
- Managerial Economics Assignment Help
- Econometrics Assignment Help
- Microeconomics Assignment Help
- Business Economics Assignment Help
- Marketing Plan Assignment Help
- Demand Supply Assignment Help
- Comparative Analysis Assignment Help
- Health Economics Assignment Help
- Macroeconomics Assignment Help
- Political Economics Assignment Help
- International Economics Assignments Help
-
Academic Writing Services
-
Essay Writing
- Essay Help
- Essay Writing Help
- Essay Help Online
- Online Custom Essay Help
- Descriptive Essay Help
- Help With MBA Essays
- Essay Writing Service
- Essay Writer For Australia
- Essay Outline Help
- illustration Essay Help
- Response Essay Writing Help
- Professional Essay Writers
- Custom Essay Help
- English Essay Writing Help
- Essay Homework Help
- Literature Essay Help
- Scholarship Essay Help
- Research Essay Help
- History Essay Help
- MBA Essay Help
- Plagiarism Free Essays
- Writing Essay Papers
- Write My Essay Help
- Need Help Writing Essay
- Help Writing Scholarship Essay
- Help Writing a Narrative Essay
- Best Essay Writing Service Canada
-
Dissertation
- Biology Dissertation Help
- Academic Dissertation Help
- Nursing Dissertation Help
- Dissertation Help Online
- MATLAB Dissertation Help
- Doctoral Dissertation Help
- Geography Dissertation Help
- Architecture Dissertation Help
- Statistics Dissertation Help
- Sociology Dissertation Help
- English Dissertation Help
- Law Dissertation Help
- Dissertation Proofreading Services
- Cheap Dissertation Help
- Dissertation Writing Help
- Marketing Dissertation Help
- Programming
-
Case Study
- Write Case Study For Me
- Business Law Case Study Help
- Civil Law Case Study Help
- Marketing Case Study Help
- Nursing Case Study Help
- Case Study Writing Services
- History Case Study help
- Amazon Case Study Help
- Apple Case Study Help
- Case Study Assignment Help
- ZARA Case Study Assignment Help
- IKEA Case Study Assignment Help
- Zappos Case Study Assignment Help
- Tesla Case Study Assignment Help
- Flipkart Case Study Assignment Help
- Contract Law Case Study Assignments Help
- Business Ethics Case Study Assignment Help
- Nike SWOT Analysis Case Study Assignment Help
- Coursework
- Thesis Writing
- CDR
- Research
-
Assignment Writing
-
Resources
- Referencing Guidelines
-
Universities
-
Australia
- Asia Pacific International College Assignment Help
- Macquarie University Assignment Help
- Rhodes College Assignment Help
- APIC University Assignment Help
- Torrens University Assignment Help
- Kaplan University Assignment Help
- Holmes University Assignment Help
- Griffith University Assignment Help
- VIT University Assignment Help
- CQ University Assignment Help
-
Australia
- Experts
- Free Sample
- Testimonial
ENEM28003 Fluid Power Engineering & Control Assignment Sample
Assignment Brief
1. Introduction
There are three main methods of transmitting power: mechanical, electrical and fluid power. Fluid power systems can transmit power more economically over greater distance. The work is accomplished by a pressurized fluid bearing directly on an operating fluid cylinder. A fluid cylinder produces a force resulting in linear motion. The fluid power systems are well suited in many industries because of their many advantages: easy and accuracy of control, multiplication of force, constant force or torque and simplicity, safety and economy.
Figure 1 presents a fluid power hydraulic press system. The purpose of this circuit is to control motion of the cylinder. The cylinder must extend, bottom out and hold pressure on the plates for some fixed period of time. During this time, pressure must be maintained in order to maintain the contact pressure between the plates (Figure 1b). The popular applications are bonding two pieces of metal together with an adhesive, holding a mold closed while the material is setting, etc.
Figure 1: Hydraulic press circuit (part) (Johnson, 2002)
If pressure is to be maintained, the directional control valve (DVC) must be left in the extended position even after the cylinder is fully extended (Figure 1b). Whenever the cylinder is bottomed out, the flow of oil is going over the pressure relief valve. This is a wastage of fluid power. This study should focus on how to manage the wastage of fluid power. This can be achieved by inserting additional parts into the fluid circuit diagram.
Simulation of a hydraulic circuit in Matlab is a good way to study and analyse the hydraulic circuits you design. In Matlab, you have to use SimScape (Simhydraulic). You have to go to Fluids, then Hydraulics (isothermal). From the library menu, you can draw the circuit. This menu has various
components needed to construct a fluid circuit diagram. By choosing the right components, the hydraulic symbols are assembled for analysis.
2. Aims
The aim of this project is to exercise your theoretical knowledge of fluid power systems and skills in practical applications in the area of mechanical and process engineering using Simscape in Simulink (Matlab).
3. Scope
You are required to study, analyse and assess an existing conventional hydraulic press system considering information available (you can assume some reasonable necessary data). Then design a new hydraulic press system or modify the existing design that has better performance. This is a team submission and each team must present their findings in a week 6 workshop session.
Your submission should have the following items and headings:
(1) Introduction to fluid power systems relating to hydraulic press systems
(2) Literature review on Conventional hydraulic press systems using standard papers from journals, conferences, books and reports
(3) Working principles of existing hydraulic press systems.
(4) Develop a case based on your research and develop a set of assumptions for your proposed design (operating pressure can be about 170 bars for example)
(5) Design and analysis of a new or modified hydraulic press system that gives better control: flow control, pressure control and directional control using sufficient minimum controlling devices and valves
(6) Safety check of pipes and pressure cylinders (thick-walled or thin-walled analysis)
(7) Prepare an Excel calculation sheet to put input data, standard equations, creating plots to compare
(8) Health and safety practices required for maintaining the system.
(9) Use proper drafting tools to show changes in your new design.
(10) Draw necessary fluid circuit diagrams
(11) Apply SimScape and carry out an analysis of your new design: piston positions, velocity, flow rate etc. vs time. Verify your simulation results.
(12) Preparation of team report and submit it in the Moodle link as per the due date.
Your report must include an executive summary, scope and objectives, methodology, schematic diagrams where necessary, discussions and concluding remarks, and references in the Harvard system.
4. Submission: It is a team submission. The due date is Friday midnight, week 6. The completed team charter document with signature will be with the team report (2nd page).
5. Reference: Introduction to Fluid Power, James L. Johnson, 2002.
Solution
Introduction
The hydraulic circuits you create can be studied and analysed by simulating them in Matlab. SimScape must be used with Matlab (Simhydraulic). Fluids must be selected before Hydraulics (isothermal). Construct the circuit using the library menu. The many items on this menu can be used to build a fluid schematic diagram. The hydraulic signals are put together for evaluation by picking the appropriate parts.One of the earliest types of machine tools is really the hydraulic press. is well suited for press operations in its current guise, from coining jewellery to forging aircraft parts. Today, industrial structural steel forming is frequently done with hydraulic incremental forming presses. Those machines are especially valued by small drawn component customers and manufacturers to the auto sector due to its high degree of process formability. vast variety of manufactured objects' shapes An effort is being made in the current systematic review to analyse the earlier research that has been done in the various structural design and analysis methodologies of hydraulic press(Huang, et al., 2019). One of the production processes, metal formation is primarily carried out on hydraulic presses. A compression moulding machine operates with an impact force. Some injection molds receive stress concentration and some parts experience longitudinal stress as a result of ongoing impact load. A CAD tool and a FEA tool like ANYSYS Keywords- Optimisation can be used to optimise the machinery framework, which is necessary to solve this issue(Adesina 2018).
Literature Review
Using physical processes and differential calculations, finite element analysis is the act of analysing a structural system in order to forecast its responds and behaviours. Determining internal forces, tensions, and genetic abnormalities of structures under diverse rates are high is the primary goal of structural analysis. Engineering's structural design division deals with structures made up of various structural elements. These elements, which are joined by pins or fixed joints, can be categorised as either bridge or frame components. In recent years, design approach has grown in importance as a tool for design professionals(Rani, et al. 2021). With the adoption of greater kinds of optimization by the industry, constructions are getting lighter, tougher, and more affordable. By maximising the weight of the material used to construct the building, using the best resources feasible while designing the compression moulding component can result in cost reductions. The quantity of the product, the price of the press, and its portability have all been attempted to be decreased. A 2D nonlinear magneto-mechanical study of an electrical motor using finite elements was presented by Errol et al. The proposed technique permits the accurate simulation of the whole switching cycle of a toggling, short stroke magnetic actuator(Yang, et al. 2018).
In the modern engineering sector, this kind of problem solving and product improvement is now an essential component of the system design. Since the development of mathematical analysis in the 1670s, optimizing has had a mathematical foundation. All contemporary manufacturing companies are working hard to create lighter, more outlay goods that also meet design, operational, and reliability requirements. In this situation, product design procedures that we all have researched in the literature are becoming more and more attractive thanks to structural optimization methods like topology and shape optimization. A corporation must upgrade its designs in order to compete on a worldwide scale. Additionally, saving is crucial for their upcoming endeavours(Wang and Chen 2022).
Finding the structure with both the best objective in light of a set of criteria is demonstrated in the following optimization. Design variables were entered used in the optimization. Challenging to create can be subdivided into many subfields depends on the type that the input variables are represented by. The performance parameters in form optimization are parameters that affect how the structure's boundary is shaped in part. When sizing characteristics like merge area, girder or stacking sequence are manipulated variable, we talk about size optimization. Topology optimization seems to be the structural mechanics subfield with the broadest use.A hydraulic press is a device that produces compressive stress using an air compressor(Luo, et al. 2018). The hydraulic press's major parts are its frame, hydraulic cylinder, and pressed table. In this assignment, the design technique was used to create the press frame, cylindrical, and press table. To enhance their effectiveness and quality for press operating operation, they are examined. By maximising the strength of the product used to construct the building, to use the best resources feasible while developing the hydraulic press sections can result in cost reduction. The quantity of the content has been attempted to be decreased in this way. Therefore, in this research, we take into account a mass optimization project for an H-frame hydraulic press used in industry(Du, et al. 2019).
Methodology
In addition to meeting a number of crucial requirements, this press must adjust for forces operating on the operating plates. Here, we employ implementation to analyse and improve the hydraulic press. In order to make the process of manufacturing small components in large quantities easier, this study aims to combine the hydraulic press's mechanical and hydraulic systems. Time constraints are a key factor in the current environment for the successful completion of any manufacturing operation. Therefore, with the help of automation, the manufacturing time may be cut down while also increasing accuracy because less human work is required. With the use of these tools, an effort has been made to ensure the quick and efficient operation of press work(Hua, et al. 2021). A hydraulic press is a device that generates force by pressurising fluids. These devices consist of a straightforward cylinder and piston system. A huge cylinder and a large piston make up the press, along with a smaller cylinder and a smaller piston. A pipe links the two cylinders, the huge one being larger than the smaller one. The pipe separating the two cylinders and indeed the two cylinders are both filled by liquid. At about this moment, Pascal's Principle governs how the hydraulic press works for assignment help.
In a device known as a Press, working forces are organised, directed, and managed. Thus, employing the hydraulic component in the press machine, an effort is made to two sounds the operation of press labour. The output signals of the mechanical machinery and rotary encoder are entirely electromechanical, such as spinning shafts or reciprocating plungers. The main benefit of putting this system into place is the ability to move heavy machinery. This movements can be started by hydraulic power, which can take the shape of a lever for human application or switching for automatic operation. Additionally, direction control systems have been installed to help regulate the orientations of piston motions. In a hydraulic press system, a liquid—typically crude oil—is pumped deep below under intense pressure to power a jet pump or a revolving pump. This pumping technology is very adaptable and could be used to create wells with low to high volumes. This technology has a greater fluid production capacity than the conventional lift pump. A hydraulic lift employs a pump to deliver oil under extreme pressure. The liquid is pushed to the bottom of the piston to lift it out of its seat by the pump pressure, that is typically between 300 as well as 400 kilograms per square centimeter. This lifts the load attached to the compressor assembly's head comparatively. To keep running, the necessary power oil or created water is recovered and reused(Du, et al. 2019.
Results
The hydraulic press and hydraulic system function similarly since they both rely on Pascal's Law for their operation. A hydraulic press is made up of the fundamental parts of a hydraulic system, such as a cylinders, pistons, pneumatic pipes, etc. This press operates in a fairly straightforward manner. The fluid (often oil) is pumped into the cylinder with the different radius in the system, which consists of two cylinders. The slave cylinders is the name given to this cylinder.This cylinder's piston is pushed, compressing the fluid inside it as it passes throughout a pipe and into the bigger cylinder. Master cylinder refers to the larger cylinders. The master pneumatic cylinder piston forces the fluid back to the previous reservoir as the pressure is applied to the ratio of the diameter. When the smaller cylinder is pushed into the hydraulic pump, the pressure the larger fuel tank applied to the fluids is increased. The hydraulic press is mostly employed in industries where wire mesh sheets need to be compressed under strong pressure. With both the aid of the press plates and the material being worked on, a professional hydraulic press can crush or compress the substance .
Discussion
A mechanical device used to lift or compress heavy objects is called a hydraulic press. Hydraulics is used to provide the force in order to boost the power of a basic mechanical level. The normal setting for this kind of machine is a factory setting. The NASA website has a decent explanation of "pressure vessels" and Pascal's Law, which may be the foundation of hydraulics. I have transcribed it here. In hydraulic pumps, forces are transferred from one area to another inside an incompressible viscous fluid, including water and oil.Hydraulic presses are 3-D complicated structures that are difficult and night before going to bed to analyse using a precise analytical method for stress and hyper - parameters. A reduced plane stress (PS) FEM models for a 918 kN hydraulic press architecture (welded frame) has now been chosen for investigation in order to decrease core memory requirements and computing costs. The deformation and stress characteristics are fairly consistent with those found from 3-D research. The PS model of assessment has been used to compare how the structure behaves even if it is invalid for generating actual values for complicated structures. Fillet, edge slicing, the presence of apertures, the relocation of reinforcing bars, and eccentricity loading are all taken into account.
Conclusions and Recommendations
- An oil leak is one of the most frequently reported issues; you'll see oil surrounding the ram, the hose end connectors, and the hydraulic lines. Assure all connectors are snug and you have used the hydraulic press's specified oil.
- Your press may overheat due to excessive friction & pressure as well as tainted or deteriorated hydraulic fluid. In order to prevent harming the sealing materials, hydraulic presses should never exceed a degree of 150° F. Make sure not to work overtime your presses, and make absolutely sure the filtration and oil are changed frequently(Yang, et al. 2018).
- In most cases, hydraulic presses typically reach the necessary pressure levels in about a second; if it takes longer, there is likely an issue with the pump since the fluid is not getting to the ram rapidly enough. Help ensure you inspect the pump along with related components like the pressure release valve and motor to ensure that everything was in functioning order and is clean since this could be triggered by leakage or dirt becoming stuck in the fluid.
- The produced manually operated hydraulic press was made possible by adhering to the work's specified goals. The materials used to build the produced machine came from the neighbourhood. The majority of the machine's parts were fabricated using mild steel. The interoperability of the mould and die without removing the ram assembly is a crucial component of this hydraulic press.
The produced hand operated hydraulic press was made possible by adhering to the work's specified goals. The materials used to build the produced machine came from the neighbourhood. The majority of the machine's parts were fabricated using mild steel. The tunability of the mould and die while removing the ram mechanism is a crucial component of this press machine. The machine that was created is depicted in Figure, which displays a cylinder engine compartment before having a sleeve pressed into it. Machine framework, structural parts, welds, pumps, and cylinder mechanisms were examined beforehand to look for any faults or hydraulic oil leaks before machine performance was assessed.
References
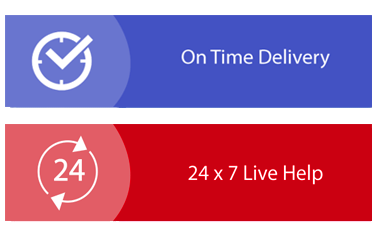
Download Samples PDF
Related Sample
- MGMT20148 Strategic Solutions for Sustainable Organisations Assignment
- BE553 Principles of International Marketing Assignment
- AP501 Food Fibre and Protein Report
- PUBH6004 Assignment 2
- BBE351A Ethics and Social Responsibility Assignment
- Digital Health and Informatics Assignment
- HLTINF001 Comply With Infection Prevention and Control Assignment
- BE955 International Marketing and Entrepreneurship Assignment
- TACC606 Accounting Business Report
- MGT501 Business Environment Assignment
- The Independent Director and Effective Corporate Governance
- Pure Gym 202202 Marketing Mid term Coursework
- GAL613 Grief and Loss Assignment
- Public Relation Portfolio Assignment
- MIS101 Information Systems for Business Assignment
- BIS3003 IS Capstone Industry Project A Assignment
- MBA5006 Managing Organisational Behaviour Assignment
- Principles of Project Management
- NURBN2024 Mental Health Recovery Plan Case Study
- Qualitative Research Methods
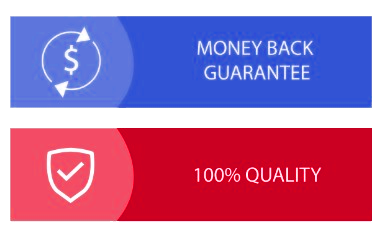
Assignment Services
-
Assignment Writing
-
Academic Writing Services
- HND Assignment Help
- SPSS Assignment Help
- College Assignment Help
- Writing Assignment for University
- Urgent Assignment Help
- Architecture Assignment Help
- Total Assignment Help
- All Assignment Help
- My Assignment Help
- Student Assignment Help
- Instant Assignment Help
- Cheap Assignment Help
- Global Assignment Help
- Write My Assignment
- Do My Assignment
- Solve My Assignment
- Make My Assignment
- Pay for Assignment Help
-
Management
- Management Assignment Help
- Business Management Assignment Help
- Financial Management Assignment Help
- Project Management Assignment Help
- Supply Chain Management Assignment Help
- Operations Management Assignment Help
- Risk Management Assignment Help
- Strategic Management Assignment Help
- Logistics Management Assignment Help
- Global Business Strategy Assignment Help
- Consumer Behavior Assignment Help
- MBA Assignment Help
- Portfolio Management Assignment Help
- Change Management Assignment Help
- Hospitality Management Assignment Help
- Healthcare Management Assignment Help
- Investment Management Assignment Help
- Market Analysis Assignment Help
- Corporate Strategy Assignment Help
- Conflict Management Assignment Help
- Marketing Management Assignment Help
- Strategic Marketing Assignment Help
- CRM Assignment Help
- Marketing Research Assignment Help
- Human Resource Assignment Help
- Business Assignment Help
- Business Development Assignment Help
- Business Statistics Assignment Help
- Business Ethics Assignment Help
- 4p of Marketing Assignment Help
- Pricing Strategy Assignment Help
- Nursing
-
Finance
- Finance Assignment Help
- Do My Finance Assignment For Me
- Financial Accounting Assignment Help
- Behavioral Finance Assignment Help
- Finance Planning Assignment Help
- Personal Finance Assignment Help
- Financial Services Assignment Help
- Forex Assignment Help
- Financial Statement Analysis Assignment Help
- Capital Budgeting Assignment Help
- Financial Reporting Assignment Help
- International Finance Assignment Help
- Business Finance Assignment Help
- Corporate Finance Assignment Help
-
Accounting
- Accounting Assignment Help
- Managerial Accounting Assignment Help
- Taxation Accounting Assignment Help
- Perdisco Assignment Help
- Solve My Accounting Paper
- Business Accounting Assignment Help
- Cost Accounting Assignment Help
- Taxation Assignment Help
- Activity Based Accounting Assignment Help
- Tax Accounting Assignment Help
- Financial Accounting Theory Assignment Help
-
Computer Science and IT
- Operating System Assignment Help
- Data mining Assignment Help
- Robotics Assignment Help
- Computer Network Assignment Help
- Database Assignment Help
- IT Management Assignment Help
- Network Topology Assignment Help
- Data Structure Assignment Help
- Business Intelligence Assignment Help
- Data Flow Diagram Assignment Help
- UML Diagram Assignment Help
- R Studio Assignment Help
-
Law
- Law Assignment Help
- Business Law Assignment Help
- Contract Law Assignment Help
- Tort Law Assignment Help
- Social Media Law Assignment Help
- Criminal Law Assignment Help
- Employment Law Assignment Help
- Taxation Law Assignment Help
- Commercial Law Assignment Help
- Constitutional Law Assignment Help
- Corporate Governance Law Assignment Help
- Environmental Law Assignment Help
- Criminology Assignment Help
- Company Law Assignment Help
- Human Rights Law Assignment Help
- Evidence Law Assignment Help
- Administrative Law Assignment Help
- Enterprise Law Assignment Help
- Migration Law Assignment Help
- Communication Law Assignment Help
- Law and Ethics Assignment Help
- Consumer Law Assignment Help
- Science
- Biology
- Engineering
-
Humanities
- Humanities Assignment Help
- Sociology Assignment Help
- Philosophy Assignment Help
- English Assignment Help
- Geography Assignment Help
- Agroecology Assignment Help
- Psychology Assignment Help
- Social Science Assignment Help
- Public Relations Assignment Help
- Political Science Assignment Help
- Mass Communication Assignment Help
- History Assignment Help
- Cookery Assignment Help
- Auditing
- Mathematics
-
Economics
- Economics Assignment Help
- Managerial Economics Assignment Help
- Econometrics Assignment Help
- Microeconomics Assignment Help
- Business Economics Assignment Help
- Marketing Plan Assignment Help
- Demand Supply Assignment Help
- Comparative Analysis Assignment Help
- Health Economics Assignment Help
- Macroeconomics Assignment Help
- Political Economics Assignment Help
- International Economics Assignments Help
-
Academic Writing Services
-
Essay Writing
- Essay Help
- Essay Writing Help
- Essay Help Online
- Online Custom Essay Help
- Descriptive Essay Help
- Help With MBA Essays
- Essay Writing Service
- Essay Writer For Australia
- Essay Outline Help
- illustration Essay Help
- Response Essay Writing Help
- Professional Essay Writers
- Custom Essay Help
- English Essay Writing Help
- Essay Homework Help
- Literature Essay Help
- Scholarship Essay Help
- Research Essay Help
- History Essay Help
- MBA Essay Help
- Plagiarism Free Essays
- Writing Essay Papers
- Write My Essay Help
- Need Help Writing Essay
- Help Writing Scholarship Essay
- Help Writing a Narrative Essay
- Best Essay Writing Service Canada
-
Dissertation
- Biology Dissertation Help
- Academic Dissertation Help
- Nursing Dissertation Help
- Dissertation Help Online
- MATLAB Dissertation Help
- Doctoral Dissertation Help
- Geography Dissertation Help
- Architecture Dissertation Help
- Statistics Dissertation Help
- Sociology Dissertation Help
- English Dissertation Help
- Law Dissertation Help
- Dissertation Proofreading Services
- Cheap Dissertation Help
- Dissertation Writing Help
- Marketing Dissertation Help
- Programming
-
Case Study
- Write Case Study For Me
- Business Law Case Study Help
- Civil Law Case Study Help
- Marketing Case Study Help
- Nursing Case Study Help
- Case Study Writing Services
- History Case Study help
- Amazon Case Study Help
- Apple Case Study Help
- Case Study Assignment Help
- ZARA Case Study Assignment Help
- IKEA Case Study Assignment Help
- Zappos Case Study Assignment Help
- Tesla Case Study Assignment Help
- Flipkart Case Study Assignment Help
- Contract Law Case Study Assignments Help
- Business Ethics Case Study Assignment Help
- Nike SWOT Analysis Case Study Assignment Help
- Coursework
- Thesis Writing
- CDR
- Research