Order Now
- Home
- About Us
-
Services
-
Assignment Writing
-
Academic Writing Services
- HND Assignment Help
- SPSS Assignment Help
- College Assignment Help
- Writing Assignment for University
- Urgent Assignment Help
- Architecture Assignment Help
- Total Assignment Help
- All Assignment Help
- My Assignment Help
- Student Assignment Help
- Instant Assignment Help
- Cheap Assignment Help
- Global Assignment Help
- Write My Assignment
- Do My Assignment
- Solve My Assignment
- Make My Assignment
- Pay for Assignment Help
-
Management
- Management Assignment Help
- Business Management Assignment Help
- Financial Management Assignment Help
- Project Management Assignment Help
- Supply Chain Management Assignment Help
- Operations Management Assignment Help
- Risk Management Assignment Help
- Strategic Management Assignment Help
- Logistics Management Assignment Help
- Global Business Strategy Assignment Help
- Consumer Behavior Assignment Help
- MBA Assignment Help
- Portfolio Management Assignment Help
- Change Management Assignment Help
- Hospitality Management Assignment Help
- Healthcare Management Assignment Help
- Investment Management Assignment Help
- Market Analysis Assignment Help
- Corporate Strategy Assignment Help
- Conflict Management Assignment Help
- Marketing Management Assignment Help
- Strategic Marketing Assignment Help
- CRM Assignment Help
- Marketing Research Assignment Help
- Human Resource Assignment Help
- Business Assignment Help
- Business Development Assignment Help
- Business Statistics Assignment Help
- Business Ethics Assignment Help
- 4p of Marketing Assignment Help
- Pricing Strategy Assignment Help
- Nursing
-
Finance
- Finance Assignment Help
- Do My Finance Assignment For Me
- Financial Accounting Assignment Help
- Behavioral Finance Assignment Help
- Finance Planning Assignment Help
- Personal Finance Assignment Help
- Financial Services Assignment Help
- Forex Assignment Help
- Financial Statement Analysis Assignment Help
- Capital Budgeting Assignment Help
- Financial Reporting Assignment Help
- International Finance Assignment Help
- Business Finance Assignment Help
- Corporate Finance Assignment Help
-
Accounting
- Accounting Assignment Help
- Managerial Accounting Assignment Help
- Taxation Accounting Assignment Help
- Perdisco Assignment Help
- Solve My Accounting Paper
- Business Accounting Assignment Help
- Cost Accounting Assignment Help
- Taxation Assignment Help
- Activity Based Accounting Assignment Help
- Tax Accounting Assignment Help
- Financial Accounting Theory Assignment Help
-
Computer Science and IT
- Operating System Assignment Help
- Data mining Assignment Help
- Robotics Assignment Help
- Computer Network Assignment Help
- Database Assignment Help
- IT Management Assignment Help
- Network Topology Assignment Help
- Data Structure Assignment Help
- Business Intelligence Assignment Help
- Data Flow Diagram Assignment Help
- UML Diagram Assignment Help
- R Studio Assignment Help
-
Law
- Law Assignment Help
- Business Law Assignment Help
- Contract Law Assignment Help
- Tort Law Assignment Help
- Social Media Law Assignment Help
- Criminal Law Assignment Help
- Employment Law Assignment Help
- Taxation Law Assignment Help
- Commercial Law Assignment Help
- Constitutional Law Assignment Help
- Corporate Governance Law Assignment Help
- Environmental Law Assignment Help
- Criminology Assignment Help
- Company Law Assignment Help
- Human Rights Law Assignment Help
- Evidence Law Assignment Help
- Administrative Law Assignment Help
- Enterprise Law Assignment Help
- Migration Law Assignment Help
- Communication Law Assignment Help
- Law and Ethics Assignment Help
- Consumer Law Assignment Help
- Science
- Biology
- Engineering
-
Humanities
- Humanities Assignment Help
- Sociology Assignment Help
- Philosophy Assignment Help
- English Assignment Help
- Geography Assignment Help
- Agroecology Assignment Help
- Psychology Assignment Help
- Social Science Assignment Help
- Public Relations Assignment Help
- Political Science Assignment Help
- Mass Communication Assignment Help
- History Assignment Help
- Cookery Assignment Help
- Auditing
- Mathematics
-
Economics
- Economics Assignment Help
- Managerial Economics Assignment Help
- Econometrics Assignment Help
- Microeconomics Assignment Help
- Business Economics Assignment Help
- Marketing Plan Assignment Help
- Demand Supply Assignment Help
- Comparative Analysis Assignment Help
- Health Economics Assignment Help
- Macroeconomics Assignment Help
- Political Economics Assignment Help
- International Economics Assignments Help
-
Academic Writing Services
-
Essay Writing
- Essay Help
- Essay Writing Help
- Essay Help Online
- Online Custom Essay Help
- Descriptive Essay Help
- Help With MBA Essays
- Essay Writing Service
- Essay Writer For Australia
- Essay Outline Help
- illustration Essay Help
- Response Essay Writing Help
- Professional Essay Writers
- Custom Essay Help
- English Essay Writing Help
- Essay Homework Help
- Literature Essay Help
- Scholarship Essay Help
- Research Essay Help
- History Essay Help
- MBA Essay Help
- Plagiarism Free Essays
- Writing Essay Papers
- Write My Essay Help
- Need Help Writing Essay
- Help Writing Scholarship Essay
- Help Writing a Narrative Essay
- Best Essay Writing Service Canada
-
Dissertation
- Biology Dissertation Help
- Academic Dissertation Help
- Nursing Dissertation Help
- Dissertation Help Online
- MATLAB Dissertation Help
- Doctoral Dissertation Help
- Geography Dissertation Help
- Architecture Dissertation Help
- Statistics Dissertation Help
- Sociology Dissertation Help
- English Dissertation Help
- Law Dissertation Help
- Dissertation Proofreading Services
- Cheap Dissertation Help
- Dissertation Writing Help
- Marketing Dissertation Help
- Programming
-
Case Study
- Write Case Study For Me
- Business Law Case Study Help
- Civil Law Case Study Help
- Marketing Case Study Help
- Nursing Case Study Help
- Case Study Writing Services
- History Case Study help
- Amazon Case Study Help
- Apple Case Study Help
- Case Study Assignment Help
- ZARA Case Study Assignment Help
- IKEA Case Study Assignment Help
- Zappos Case Study Assignment Help
- Tesla Case Study Assignment Help
- Flipkart Case Study Assignment Help
- Contract Law Case Study Assignments Help
- Business Ethics Case Study Assignment Help
- Nike SWOT Analysis Case Study Assignment Help
- Coursework
- Thesis Writing
- CDR
- Research
-
Assignment Writing
-
Resources
- Referencing Guidelines
-
Universities
-
Australia
- Asia Pacific International College Assignment Help
- Macquarie University Assignment Help
- Rhodes College Assignment Help
- APIC University Assignment Help
- Torrens University Assignment Help
- Kaplan University Assignment Help
- Holmes University Assignment Help
- Griffith University Assignment Help
- VIT University Assignment Help
- CQ University Assignment Help
-
Australia
- Experts
- Free Sample
- Testimonial
MEM602 Engineering Risk Management Assignment Sample
Assignment Brief
Individual/Group - Individual
Length - 2000 words +/- 10%
Learning Outcomes
The Subject Learning Outcomes demonstrated by successful completion of the task below include:
a) developing a systematic risk management approach to strategically and operationally identify, evaluate, analyses, manage and govern risks in an engineering context
b) implementing a risk management approach in engineering practice workplace situations
c) assessing and applying methodologies and tools to improve safety, reliability and to reduce hazards.
Submission - Due by 11:55pm AEST/AEDT Sunday end of Module 3.
Weighting - 30%
Total Marks - 100 marks
Task Summary – Assessment 1
For Assessment 1, you are required to develop a risk strategy. You will be required to provide a formal report in 2000 words (+/- 10%) that outlines a risk strategy for the attached Case Study. Please note, this is an individual assessment, and it is expected that you undertake appropriate academic cues in preparing your submission.
Context – Assessment 1
The Case Study provides an overview of a specialist manufacturing organization operating in NSW, Australia. A number of attributes have been provided in the Case Study to give the reviewer (i.e., you as student) the opportunity to draw on material and construct a response that is relevant to the information provided (in the Case Study). Reference to the Case Study is required for ALL three assessments, and your critique of the Case Study will differ across ALL three assessments.
For Assessment 1, you are required to develop a risk strategy for the Case Study. The Managing Director has assigned the Project Engineer (you) to develop a risk strategy for the organization. It has become apparent to senior management that whilst key personnel across the organization have independently managed their work units and processes and the risks associated with these, an in- depth review at a strategic level has yet to take place. As Project Engineer, you will be required to provide a formal report that outlines a risk strategy for the company. Your report will be broken into 4 main categories: people, reputation, business process and systems and financial. Within these categories, you will address the scope of risk: development and evaluation of good governance principles, identification of any external and internal risk-related issues (including systemic risks) and stakeholder responsibility together with risk reporting across the company and any affiliated entities. Collectively, these factors will be discussed in the four main categories to outline the role of compliance leading to the development of a compliance policy for the company and any affiliated entities. It is expected that your report will focus on these aspects and not just on reporting a risk management plan. However, risk management tools and guides such as the Hierarchy of Controls and reference to industry standards (and others if deemed necessary) can be used to support your argument.
Report structure for assignment help
1. Executive Summary (what is the purpose and nature of the report)
2. Contents page
3. Introduction — Background information
4. Body (as outlined in report criteria)
5. Conclusion
6. Recommendations
7. List of References
8. Appendices
Referencing
It is essential that you use appropriate APA style for citing and referencing research. Please see more information on referencing here: https://library.torrens.edu.au/academicskills/apa/tool
Submission Instructions
Submit this task via the Assessment link in the main navigation menu in MEM602 Engineering Risk Management. The Learning Facilitator will provide feedback via the Grade Centre in the LMS portal. Feedback can be viewed in My Grades.
Case Study
Description of organization:
MDF Manufacturing is a small to medium-size enterprise located in the Central West and Orana District of NSW, Australia. MDF provides melamine particle-board manufacturing finishing services to wholesale, specialist retail suppliers and small businesses, both intrastate and interstate. State-of-the-art machinery and manufacturing finishing techniques allow MDF to supply and compete in very competitive kitchen and decorative door, panel and laminate markets. An engineering logistics/services workshop is operated from the site. The site is situated adjacent to a major road route in a rural area governed by the Central West and Orana Municipal Council. The MDF workforce comprises 155 employees, all of whom travel to the organization for work from within the local area in their own vehicles.
Senior Management at the MDF site:
• Managing Director (Sales and Marketing)
• Regional Sales Manager
• Project Engineer
• Logistics/Purchasing Manager
Other key personnel:
• Safety Officer
• Site Supervisor
• Maintenance Supervisor
• Warehouse Day Shift Supervisor
• Accounts Manager
• Site Operators
• Maintenance Operator
• Warehouse Operators
The facility is open 6 days a week / 24 hours a day and has no recognized holiday or shut-down periods, except for wo days at Christmas and two days over the Easter vacation periods.
Site setting:
Founded in 1985, the site comprises a shared maintenance garage, engineering logistics/services workshop, open-air vehicle parking, manufacturing/finishing complex and a single-storey office block situated on a formerly green-field site. To the North, there is arable farmland with 25-metre poplar trees along the boundary fence. On the Eastern boundary, there is a separate organization specializing in haulage and logistics. To the South, there is a service road, which acts as the main access road for vehicles to and from the site to the major road route and local country lanes. The Western boundary is separated by a small stream, used by anglers throughout the season. The site has a 3- metre-high mesh fence around the perimeter and a barrier at the main entrance.
Utilities:
Heating for the garage, manufacturing complex and offices is provided by natural gas. Part of the Manufacturing complex has comprehensive vented ducting with controlled airflow systems driven by electrical power.
Water: 16,000 m3 per year received from municipal supply. It is used in manufacturing processes, shared maintenance garage, wash-off, cleaning, heating, and so on.
Electricity: 1,800,000 Kwh per year.
Wastes: Solid waste from the manufacturing operation is collected from the workshop and shared garage operations, and placed in skips for transfer to the local waste disposal site. Of all the manufacturing maintenance waste – oil, filters, worn components, processing waste from manufacturing equipment and fume extraction (low Formaldehyde emitting) – some is segregated, recycled, and extracted by approved sub-contractors. Solid wastes are stored in skips on compacted ground bordered by unsurfaced soil. Liquid wastes are stored in 205-litre drums in the same area.
Fuel:
Diesel fuel is delivered to the site on contract and stored in two 30,000-litre elevated tanks located against the western boundary and surrounded with bunding (secondary containment) of a 110% capacity. This arrangement is shared with the Haulage and Logistics Operation.
Activities:
1. Primary finishing: trimming, sanding and upgrading of the plywood after pressing, is undertaken so as to enhance the marketability of the product.
2. Trimming saws cut the plywood boards to the required size, which are then sanded in machines fitted with wide-belt or drum sanders so as to obtain the desired surface smoothness.
3. Plywood is then produced in a wide range of sizes and thicknesses.
4. The product is sorted, packaged and allocated into lots ready for transport.
Solution
1. Introduction
The report focuses on the risk strategy of MDF, a small-scale manufacturing organization that supplies melamine products to retailers, wholesalers and suppliers across various states. This report discusses a risk strategy concerning people, organizational reputation, business process, and finances. During the Covid-19 pandemic Australian government as well as SMEs increase their expenditure in order safeguard the life of people that seems utmost crucial to increase the organizational reputation (Referred to the Appendix 1). The scope of risk is identified by developing and evaluating a good governance principle. The risk-related issues concerning the internal and external environment will be discussed in the report. The compliance policy and risk assessment through stakeholder responsibility will be provided in this report.
2. Risk Strategy
Risks privileged in several aspects
People-Working in the manufacturing sector has some hazards associated with it. The natural gas supply provides the heating of the garage, and the leakage may have some hazardous effect on the environment. Exposure to natural gas can have a life-threatening impact on employees. In this regard, it is found that mainly four types of natural gases are existing in Australia which are shale gas, tight gas, coal seam gas and conventional gas (Referred to the Appendix 2).
Reputation- Solid waste management is an important part of business as environmental pollution is an alarming problem. The organization performs its solid waste management process as many materials from the garage, and the workshop is collected. Approved contractors recycle the waste like oil, filters, the processing. If any negligence takes place in this regard, the reputation of the organization will suffer. Public-private partnership organizations suffer from risks like inflation, corruption, delay in completion, exchange and interest rate fluctuation. They release their waste to the disposal site locally, failing which may degrade their market value. They offer melamine particle board to suppliers, retailers both in a small and medium-sized business. The quality needs to be maintained. Otherwise, they may lose their business.
Business processes and system- The business process risks may include labor cost, transportation and logistics, inventory management, supply chain and regulatory or trade policies. Purchasing organizations are exposed to risk in their interaction with the suppliers (Osei-Kyei&Chan,2017). The task associated with the site is fuel storage and refueling, surface water discharge, water storage and disposal and compression planning. All these issues need to be properly handled; otherwise, storage pipe leakages can cause serious damage to the organization.
Financial risk-The budget of the raw materials and the cost of labor are some of the issues that may lead to serious issues later. The raw materials are natural gas for heating the garage and other materials used for preparing melamine products if the budget exceeds due to wastage and low quality of the materials, which is a potential risk for the organization.
3. Scope of Risk
3.1. Development and Evaluation of governance principle
The governance principles for a risk management plan are:
• Identify and assess the factors that are related to the risk.
• Evaluate the likelihood for risk to occur
• Develop strategies to mitigate the risk factors.
• Prepare a risk management plan.
• Evaluate the strategies of risk management.
The security governance policies must have some rules and regulatory principles that offer compliance to the industry and the organizational laws. International Risk Governance Council includes the economic, social, cultural perspectives of risk and develops plan through communication with stakeholders and involvement (der Vegt,2018). It is necessary to inform all the internal and external stakeholders regarding the policies, and everyone should abide by the industry standards related to risk strategy.
Evaluating the principles
A good governance principle must be participatory, efficient, responsive, effective, consensus-oriented, equitable, responsible and inclusive. For evaluating the process, proper testing of the principles needs to be performed, which is achieved by collecting information from the stakeholders of the organization. Interview, survey methods, and questionnaires are ways of collecting feedback from the employees and other shareholders. Their opinion will help assess the risk management plan's effectiveness, and any necessary alterations can be implemented. Past experiences and information from the market can help make good governance policies that reduce the probability of any hazards or risk associated with a business process. Enterprise Risk Management Plan is gaining popularity and induced by regulatory requirements (Sax &Andersen,2019). The risk can be operational where there is some flaw in the working process of the organization or failure of management or financial crisis. A proper evaluation and development of governance principles will help in identifying and mitigating the risks. For NDF, governance policy must define the ways of dealing with solid waste and the use of natural gas without any accident.
3.2. Identification of the internal and external risk-related issue
In the business of MDF, there are several internal and external risk-related issues. Firstly, the company may face issues to maintain business operations properly due to the shortage of employees. It is observed that there are only 155 employees in MDF to manage business operations. However, the company is associated with various activities such as trimming plywood, upgrading it, sanding and others. Therefore, it is a significant risk in the business of the company.
Along with this, wastes from the business is another internal business risk of MDF. For this purpose, the company needs to adopt a specific policy for waste management to maintain solid waste, worn components, oil, filters and so on. This waste can impact the environment of the industry negatively and may reduce the competitive advantage of MDF.
On the contrary, some external risk is associated with the businesses of MDF also. It is noticed that there are several particleboard manufacturing companies in Australia, such as D&R Henderson, Famitchell and others. That is why the existence of many leading particleboard manufacturing companies is a significant risk. MDF has to develop its business strategy accordingly to sustain its profitability among other competitors.
3.3. Stakeholder responsibility in the risk reporting across MDF and affiliated entities
As Hein et al. (2017) mentioned, stakeholder refers to the people interested in business activities and operations. Business risk affects the stakeholder interest of companies. That is why the stakeholder is responsible for the risk reporting and needs to help in the strategy for overcoming the risk. The major stakeholders of MDF are the key employees, suppliers, warehouse operators and others. Therefore, the CEO of MDF needs to report to the stakeholders about the potential risk of business in risk reporting.
The affiliated entity in the organization is the direct or indirect control of another entity. The other entity could be the subsidiary company or parent company. However, considering the business risk of MDF, it can be stated that the company would be beneficial with the entry of the subsidiary company. Through this, it would be possible to maintain the company's business activities properly with the help of the other organization. As subsidiary companies are other major stakeholders of the organization, the risk report of MDF is presented to the stakeholders to mitigate the company's risk significantly.
4. Role of the compliance for MDF and affiliated entities
Compliance in business refers to the relevant laws and regulations which organizations have to follow. In the view of Fiandrino, Busso&Vrontis (2019) compliance identifies the risk of the organization and assesses them properly. As there are many risks associated with the business of MDF; therefore, compliance plays a vital role in the business of MDF. The rules and regulations of MDF need to be implemented properly to avoid such risk. In Australia, there is a fair work act of 2009, which has to be followed to maintain the minimum standard of employment and entitlement in the country. Through following this, it is possible to retain the employees and improve the effectiveness of the company. As it is mentioned that there are many business activities in the business of MDF. Therefore, retaining the employee base will be effective to manage all the operations properly. Another major importance of compliance in business is, it helps to monitor the effectiveness of the risk management and help in the risk exposure. It is noticed that MDF has different employers for managing different business activities such as safety officer, site operator, accounts manager and others. Therefore, considering this, it can be stated that MDF has the proper resources to manage the potential risk and to develop the manufacturing operation.
Entity compliance defines the process and practices of business with regulatory and financial compliance. It is mentioned that through a subsidiary entity of another company in the business of MDF, the company can achieve maximum outcome business. In this case, compliance will help associate the other company in the business of MDF in a proper legal manner. Hence, compliance has an effective role in the business of MDF and the affiliated entity.
5. Compliance policy of the company and affiliated entities
As Haugh (2017) stated, corporate compliance refers to the internal policy and procedures for preventing the employees from violations of ethical standards, regulations, and others. In this way, compliance policy is involved with the risk management and internal monitoring and control of the organization legally. Considering this, it can be mentioned that the MDF needs to follow the Corporations Act of 2001 for managing their business in the market of Australia. Following the proper compliance policy will help manage the people, activities, finance and other aspects of the organization. A proper compliance policy enables the MDF to monitor and control the internal business process of the company. It effectively reduces the legal issues of the organizations and will enhance the public relation of MDF with their employees and other stakeholders. Along with this, as it is observed that the shortage of employees is a major issue of the organization; therefore, compliance policy will foster the employees' trust towards the organization and be effective in retaining the employee base for managing the organizational activities.
The compliance policy of MDF needs to be applied in the affiliated entity of the organization as well. By applying proper compliance policy, the association of the MDF with other organizations could be generated legally. As MDF is a small to medium-sized particleboard manufacturing company in Australia, an affiliated entity in the organization will enable the company to achieve a huge customer base and be effective in developing the market. Along with this, compliance policy will improve the organizational and operational efficiency of MDF and, in this way, will provide a significant competitive advantage for the organization. That is why, to manage the risk in the business of MDF, adopting a proper compliance policy is important.
6. Conclusion
From the report, it can be concluded that a risk mitigation plan is essential for an organization. Good governance policies are necessary for evaluating a risk management plan. The stakeholder responsibility is associated with proper governance of the plan, and the duties and responsibilities need to be clearly stated. A compliance plan that supports industry standards helps manage the risk associated with the business. A recommendation plan is developed for the risk strategy that will help NDF gain insight into the internal and external issues and eliminate the factors that are re-associated with a risk management plan.
7. Recommendations
• It is necessary to remain open to any changes that are required in future as the future is unpredictable, and any unprecedented risk may surface in future.
• The organisational culture is an important aspect where the stakeholders must learn from their mistakes and ready to change whenever necessary.
• The duties and responsibilities of each stakeholder must be properly stated. The governance principles must provide a clear description of the risk management policies and techniques associated with the potential factors of risk.
• A proper strategy is essential for risk assessment, and professionals need to be introduced to make an effective policy.
• The internal control, policy governance and quality control, and security issues need to be properly handled by the organisation's key personnel.
• MDF uses the open area for vehicles, and they offer natural gas as a source of energy. Instead of that, using renewable energy resources will help in dealing with environmental issues.
• Solid waste needs to be recycled, and the disposal process must follow e-waste management procedures governed by state laws.
• Cost overrun is a major reason for project failure. Some factors like low advance payment, use of innovative technology, unclear specifications are some of the reasons that are related to chaos (Afzal et al. 2019). It is necessary to keep the project under the propped budget through proper policies and governance.
References
Afzal, F., Yunfei, S., Sajid, M., & Afzal, F. (2019). Integrated priority decision index for risk assessment in chaos: cost overruns in transport projects. Engineering, Construction and Architectural Management, 27(4), 825–849. https://doi.org/10.1108/ECAM-02-2019-0079
Der Vegt, R. G. (2018). Risk assessment and risk governance of liquefied natural gas development in Gladstone, Australia. Risk Analysis, 38(9), 1830–1846. https://doi.org/10.1111/risa.12977
Fiandrino, S., Busso, D., &Vrontis, D. (2019). Sustainable responsible conduct beyond the boundaries of compliance. British Food Journal, 121(5), 1035–1049. https://doi.org/10.1108/BFJ-03-2019-0182
Haugh, T. (2017). Nudging corporate compliance. American Business Law Journal, 54(4), 683–741. https://doi.org/10.1111/ablj.12109
Hein, A. M., Jankovic, M., Feng, W., Farel, R., Yune, J. H., &Yannou, B. (2017). Stakeholder power in industrial symbioses: a stakeholder value network approach. Journal of Cleaner Production, 148, 923–933. https://doi.org/10.1016/j.jclepro.2017.01.136
Osei-Kyei, R., & Chan, A. P. C. (2017). Risk assessment in public-private partnership infrastructure projects. Construction Innovation, 17(2), 204–223. https://doi.org/10.1108/CI-08-2016-0043
Sax, J., & Andersen, T. J. (2019). Making risk management strategic: integrating enterprise risk management with strategic planning. European Management Review, 16(3), 719–740. https://doi.org/10.1111/emre.12185
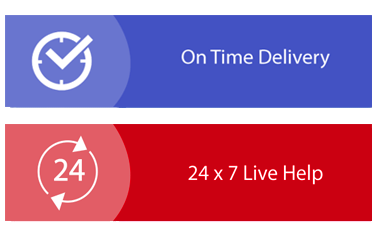
Download Samples PDF
Related Sample
- MIS301 Cyber Security Assignment
- CLWM4000 Business and Corporations Law Assignment
- BSBCRT611 Apply Critical Thinking for Complex Problem Solving Assignment
- BE486 Organisational Behaviour and Human Resource Management Assignment
- LAWS20058 Australian Commercial Law Assignment
- ITECH1103 Big Data and Analytics Assignment
- MIS500 Foundations of Information Systems Assignment
- INF60007 Business Information System Assignment
- Design Management Audit and Employee Engagement Plan Assignment
- Marketing Assessment Situation Analysis
- PBHL20010 Case study Assignment
- Do Psychopaths Have Abnormal Brains Assignment
- Qualitative Research Methods
- MBA613 Organisational Change and Innovation Case Study
- BDA601 Big Data and Analytics Case Study
- AP501 Food Fibre and Protein Report
- MGT602 Business Decision Making Process Case Study
- MBAS905 Advanced Business Analytics Case Study 1
- PMN610 Project Management Principles Assignment
- SOAD9206 Social Work Research in Practice Settings Report 1
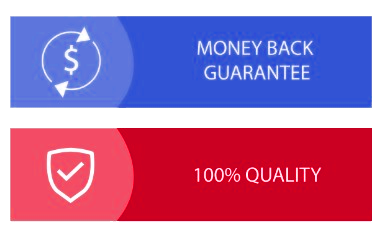
Assignment Services
-
Assignment Writing
-
Academic Writing Services
- HND Assignment Help
- SPSS Assignment Help
- College Assignment Help
- Writing Assignment for University
- Urgent Assignment Help
- Architecture Assignment Help
- Total Assignment Help
- All Assignment Help
- My Assignment Help
- Student Assignment Help
- Instant Assignment Help
- Cheap Assignment Help
- Global Assignment Help
- Write My Assignment
- Do My Assignment
- Solve My Assignment
- Make My Assignment
- Pay for Assignment Help
-
Management
- Management Assignment Help
- Business Management Assignment Help
- Financial Management Assignment Help
- Project Management Assignment Help
- Supply Chain Management Assignment Help
- Operations Management Assignment Help
- Risk Management Assignment Help
- Strategic Management Assignment Help
- Logistics Management Assignment Help
- Global Business Strategy Assignment Help
- Consumer Behavior Assignment Help
- MBA Assignment Help
- Portfolio Management Assignment Help
- Change Management Assignment Help
- Hospitality Management Assignment Help
- Healthcare Management Assignment Help
- Investment Management Assignment Help
- Market Analysis Assignment Help
- Corporate Strategy Assignment Help
- Conflict Management Assignment Help
- Marketing Management Assignment Help
- Strategic Marketing Assignment Help
- CRM Assignment Help
- Marketing Research Assignment Help
- Human Resource Assignment Help
- Business Assignment Help
- Business Development Assignment Help
- Business Statistics Assignment Help
- Business Ethics Assignment Help
- 4p of Marketing Assignment Help
- Pricing Strategy Assignment Help
- Nursing
-
Finance
- Finance Assignment Help
- Do My Finance Assignment For Me
- Financial Accounting Assignment Help
- Behavioral Finance Assignment Help
- Finance Planning Assignment Help
- Personal Finance Assignment Help
- Financial Services Assignment Help
- Forex Assignment Help
- Financial Statement Analysis Assignment Help
- Capital Budgeting Assignment Help
- Financial Reporting Assignment Help
- International Finance Assignment Help
- Business Finance Assignment Help
- Corporate Finance Assignment Help
-
Accounting
- Accounting Assignment Help
- Managerial Accounting Assignment Help
- Taxation Accounting Assignment Help
- Perdisco Assignment Help
- Solve My Accounting Paper
- Business Accounting Assignment Help
- Cost Accounting Assignment Help
- Taxation Assignment Help
- Activity Based Accounting Assignment Help
- Tax Accounting Assignment Help
- Financial Accounting Theory Assignment Help
-
Computer Science and IT
- Operating System Assignment Help
- Data mining Assignment Help
- Robotics Assignment Help
- Computer Network Assignment Help
- Database Assignment Help
- IT Management Assignment Help
- Network Topology Assignment Help
- Data Structure Assignment Help
- Business Intelligence Assignment Help
- Data Flow Diagram Assignment Help
- UML Diagram Assignment Help
- R Studio Assignment Help
-
Law
- Law Assignment Help
- Business Law Assignment Help
- Contract Law Assignment Help
- Tort Law Assignment Help
- Social Media Law Assignment Help
- Criminal Law Assignment Help
- Employment Law Assignment Help
- Taxation Law Assignment Help
- Commercial Law Assignment Help
- Constitutional Law Assignment Help
- Corporate Governance Law Assignment Help
- Environmental Law Assignment Help
- Criminology Assignment Help
- Company Law Assignment Help
- Human Rights Law Assignment Help
- Evidence Law Assignment Help
- Administrative Law Assignment Help
- Enterprise Law Assignment Help
- Migration Law Assignment Help
- Communication Law Assignment Help
- Law and Ethics Assignment Help
- Consumer Law Assignment Help
- Science
- Biology
- Engineering
-
Humanities
- Humanities Assignment Help
- Sociology Assignment Help
- Philosophy Assignment Help
- English Assignment Help
- Geography Assignment Help
- Agroecology Assignment Help
- Psychology Assignment Help
- Social Science Assignment Help
- Public Relations Assignment Help
- Political Science Assignment Help
- Mass Communication Assignment Help
- History Assignment Help
- Cookery Assignment Help
- Auditing
- Mathematics
-
Economics
- Economics Assignment Help
- Managerial Economics Assignment Help
- Econometrics Assignment Help
- Microeconomics Assignment Help
- Business Economics Assignment Help
- Marketing Plan Assignment Help
- Demand Supply Assignment Help
- Comparative Analysis Assignment Help
- Health Economics Assignment Help
- Macroeconomics Assignment Help
- Political Economics Assignment Help
- International Economics Assignments Help
-
Academic Writing Services
-
Essay Writing
- Essay Help
- Essay Writing Help
- Essay Help Online
- Online Custom Essay Help
- Descriptive Essay Help
- Help With MBA Essays
- Essay Writing Service
- Essay Writer For Australia
- Essay Outline Help
- illustration Essay Help
- Response Essay Writing Help
- Professional Essay Writers
- Custom Essay Help
- English Essay Writing Help
- Essay Homework Help
- Literature Essay Help
- Scholarship Essay Help
- Research Essay Help
- History Essay Help
- MBA Essay Help
- Plagiarism Free Essays
- Writing Essay Papers
- Write My Essay Help
- Need Help Writing Essay
- Help Writing Scholarship Essay
- Help Writing a Narrative Essay
- Best Essay Writing Service Canada
-
Dissertation
- Biology Dissertation Help
- Academic Dissertation Help
- Nursing Dissertation Help
- Dissertation Help Online
- MATLAB Dissertation Help
- Doctoral Dissertation Help
- Geography Dissertation Help
- Architecture Dissertation Help
- Statistics Dissertation Help
- Sociology Dissertation Help
- English Dissertation Help
- Law Dissertation Help
- Dissertation Proofreading Services
- Cheap Dissertation Help
- Dissertation Writing Help
- Marketing Dissertation Help
- Programming
-
Case Study
- Write Case Study For Me
- Business Law Case Study Help
- Civil Law Case Study Help
- Marketing Case Study Help
- Nursing Case Study Help
- Case Study Writing Services
- History Case Study help
- Amazon Case Study Help
- Apple Case Study Help
- Case Study Assignment Help
- ZARA Case Study Assignment Help
- IKEA Case Study Assignment Help
- Zappos Case Study Assignment Help
- Tesla Case Study Assignment Help
- Flipkart Case Study Assignment Help
- Contract Law Case Study Assignments Help
- Business Ethics Case Study Assignment Help
- Nike SWOT Analysis Case Study Assignment Help
- Coursework
- Thesis Writing
- CDR
- Research