Order Now
- Home
- About Us
-
Services
-
Assignment Writing
-
Academic Writing Services
- HND Assignment Help
- SPSS Assignment Help
- College Assignment Help
- Writing Assignment for University
- Urgent Assignment Help
- Architecture Assignment Help
- Total Assignment Help
- All Assignment Help
- My Assignment Help
- Student Assignment Help
- Instant Assignment Help
- Cheap Assignment Help
- Global Assignment Help
- Write My Assignment
- Do My Assignment
- Solve My Assignment
- Make My Assignment
- Pay for Assignment Help
-
Management
- Management Assignment Help
- Business Management Assignment Help
- Financial Management Assignment Help
- Project Management Assignment Help
- Supply Chain Management Assignment Help
- Operations Management Assignment Help
- Risk Management Assignment Help
- Strategic Management Assignment Help
- Logistics Management Assignment Help
- Global Business Strategy Assignment Help
- Consumer Behavior Assignment Help
- MBA Assignment Help
- Portfolio Management Assignment Help
- Change Management Assignment Help
- Hospitality Management Assignment Help
- Healthcare Management Assignment Help
- Investment Management Assignment Help
- Market Analysis Assignment Help
- Corporate Strategy Assignment Help
- Conflict Management Assignment Help
- Marketing Management Assignment Help
- Strategic Marketing Assignment Help
- CRM Assignment Help
- Marketing Research Assignment Help
- Human Resource Assignment Help
- Business Assignment Help
- Business Development Assignment Help
- Business Statistics Assignment Help
- Business Ethics Assignment Help
- 4p of Marketing Assignment Help
- Pricing Strategy Assignment Help
- Nursing
-
Finance
- Finance Assignment Help
- Do My Finance Assignment For Me
- Financial Accounting Assignment Help
- Behavioral Finance Assignment Help
- Finance Planning Assignment Help
- Personal Finance Assignment Help
- Financial Services Assignment Help
- Forex Assignment Help
- Financial Statement Analysis Assignment Help
- Capital Budgeting Assignment Help
- Financial Reporting Assignment Help
- International Finance Assignment Help
- Business Finance Assignment Help
- Corporate Finance Assignment Help
-
Accounting
- Accounting Assignment Help
- Managerial Accounting Assignment Help
- Taxation Accounting Assignment Help
- Perdisco Assignment Help
- Solve My Accounting Paper
- Business Accounting Assignment Help
- Cost Accounting Assignment Help
- Taxation Assignment Help
- Activity Based Accounting Assignment Help
- Tax Accounting Assignment Help
- Financial Accounting Theory Assignment Help
-
Computer Science and IT
- Operating System Assignment Help
- Data mining Assignment Help
- Robotics Assignment Help
- Computer Network Assignment Help
- Database Assignment Help
- IT Management Assignment Help
- Network Topology Assignment Help
- Data Structure Assignment Help
- Business Intelligence Assignment Help
- Data Flow Diagram Assignment Help
- UML Diagram Assignment Help
- R Studio Assignment Help
-
Law
- Law Assignment Help
- Business Law Assignment Help
- Contract Law Assignment Help
- Tort Law Assignment Help
- Social Media Law Assignment Help
- Criminal Law Assignment Help
- Employment Law Assignment Help
- Taxation Law Assignment Help
- Commercial Law Assignment Help
- Constitutional Law Assignment Help
- Corporate Governance Law Assignment Help
- Environmental Law Assignment Help
- Criminology Assignment Help
- Company Law Assignment Help
- Human Rights Law Assignment Help
- Evidence Law Assignment Help
- Administrative Law Assignment Help
- Enterprise Law Assignment Help
- Migration Law Assignment Help
- Communication Law Assignment Help
- Law and Ethics Assignment Help
- Consumer Law Assignment Help
- Science
- Biology
- Engineering
-
Humanities
- Humanities Assignment Help
- Sociology Assignment Help
- Philosophy Assignment Help
- English Assignment Help
- Geography Assignment Help
- Agroecology Assignment Help
- Psychology Assignment Help
- Social Science Assignment Help
- Public Relations Assignment Help
- Political Science Assignment Help
- Mass Communication Assignment Help
- History Assignment Help
- Cookery Assignment Help
- Auditing
- Mathematics
-
Economics
- Economics Assignment Help
- Managerial Economics Assignment Help
- Econometrics Assignment Help
- Microeconomics Assignment Help
- Business Economics Assignment Help
- Marketing Plan Assignment Help
- Demand Supply Assignment Help
- Comparative Analysis Assignment Help
- Health Economics Assignment Help
- Macroeconomics Assignment Help
- Political Economics Assignment Help
- International Economics Assignments Help
-
Academic Writing Services
-
Essay Writing
- Essay Help
- Essay Writing Help
- Essay Help Online
- Online Custom Essay Help
- Descriptive Essay Help
- Help With MBA Essays
- Essay Writing Service
- Essay Writer For Australia
- Essay Outline Help
- illustration Essay Help
- Response Essay Writing Help
- Professional Essay Writers
- Custom Essay Help
- English Essay Writing Help
- Essay Homework Help
- Literature Essay Help
- Scholarship Essay Help
- Research Essay Help
- History Essay Help
- MBA Essay Help
- Plagiarism Free Essays
- Writing Essay Papers
- Write My Essay Help
- Need Help Writing Essay
- Help Writing Scholarship Essay
- Help Writing a Narrative Essay
- Best Essay Writing Service Canada
-
Dissertation
- Biology Dissertation Help
- Academic Dissertation Help
- Nursing Dissertation Help
- Dissertation Help Online
- MATLAB Dissertation Help
- Doctoral Dissertation Help
- Geography Dissertation Help
- Architecture Dissertation Help
- Statistics Dissertation Help
- Sociology Dissertation Help
- English Dissertation Help
- Law Dissertation Help
- Dissertation Proofreading Services
- Cheap Dissertation Help
- Dissertation Writing Help
- Marketing Dissertation Help
- Programming
-
Case Study
- Write Case Study For Me
- Business Law Case Study Help
- Civil Law Case Study Help
- Marketing Case Study Help
- Nursing Case Study Help
- Case Study Writing Services
- History Case Study help
- Amazon Case Study Help
- Apple Case Study Help
- Case Study Assignment Help
- ZARA Case Study Assignment Help
- IKEA Case Study Assignment Help
- Zappos Case Study Assignment Help
- Tesla Case Study Assignment Help
- Flipkart Case Study Assignment Help
- Contract Law Case Study Assignments Help
- Business Ethics Case Study Assignment Help
- Nike SWOT Analysis Case Study Assignment Help
- Coursework
- Thesis Writing
- CDR
- Research
-
Assignment Writing
-
Resources
- Referencing Guidelines
-
Universities
-
Australia
- Asia Pacific International College Assignment Help
- Macquarie University Assignment Help
- Rhodes College Assignment Help
- APIC University Assignment Help
- Torrens University Assignment Help
- Kaplan University Assignment Help
- Holmes University Assignment Help
- Griffith University Assignment Help
- VIT University Assignment Help
- CQ University Assignment Help
-
Australia
- Experts
- Free Sample
- Testimonial
PPMP20009 Leading Lean Projects Assignment Sample
The Case Study-
The case study for this assignment is the Putting Lean Principles in the Warehouse (2008).
Read and analyse this case study thoroughly to grasp and classify the information it contains.
You are encouraged to do your own research, but the following article is a compulsory reading, and its website link is provided below:
Doug Bartholomew (2008). Putting Lean Principles in the Warehouse, Lean Enterprise Institute
https://www.lean.org/the-lean-post/articles/putting-lean-principles-in-the-warehouse/
https://www.lean.org/wp-content/uploads/2021/06/312.pdf
Useful links on Lean Warehousing:
https://leanaust.com/services/lean-warehousing
https://www.orderhive.com/knowledge-center/lean-warehousing
https://igps.net/blog/2018/10/25/following-lean-warehousing-principles-improved-efficiency/
https://www.lean.org/the-lean-post/articles/think-you-know-your-warehouse-or-distribution-
center-think-again/
Assessment Tasks
You have been hired as a Lean consultant to produce a brief report on the use of Lean transformation projects for supply chain and warehouse organisations, based on the given case study.
Your submission must discuss the following topics:
1) The case study describes a business process that is different from traditional manufacturing. Using the examples from the case study or other Lean transformation projects for warehousing, explain how the following concepts of a lean framework are manifested in a warehousing project:
a) Voice of the Customer
b) Critical Customer Requirements
c) Critical to Quality
d) Critical to Process
2) Select 4 of the 8 Wastes of Lean that apply to the case study and demonstrate how each waste relates to one or more PMBOK Knowledge Areas or PRINCE2 Themes:
a) How was the waste reduced in the case study?
b) What was the effect on the project overall?
c) What tools or techniques from PMBOK or PRINCE2 were applied in achieving this?
3) Select 3 principles from the House of Lean as discussed during week 1 lecture. Demonstrate how the application of these principles helped achieve project success.
4) As a conclusion, write a short reflection on the people management aspect of the case study (transformation project) and also list 2 lessons you have learned from this case study that may help you manage people more effectively in your career.
Report Layout
The written report on the case study should be organised using the following headings and guidelines:
- Title (Cover) Page with clear details of unit code and name, student number and name, lecturer & tutor names, submission date etc.
- Table of Contents (Optional)
- Introduction (Optional)
Introduction should state the aims of the report.
Question 1 – Manifestation of Lean framework concepts in the case study
Using the examples from the case study or other Lean transformation projects for warehousing, explain how the following concepts of a lean framework are manifested in a warehousing project:
a) Voice of the Customer (VOC)
b) Critical Customer Requirements (CCR)
c) Critical to Quality (CTQ)
d) Critical to Process (CTP)
Question 2 – Elaboration of 4 Lean wastes that apply to the case study
Select 4 of the 8 Lean wastes that apply to the case study and elaborate about each waste:
a) How was the waste reduced in the case study?
b) What was the effect on the overall project?
c) What tools or techniques from PMBOK or PRINCE2 were applied in achieving this?
Question 3 – Application of 3 Lean principles on the case study
Select 3 principles from the House of Lean and demonstrate how the application of these principles helped achieve the project (case study) success.
Question 4 – Lessons learnt about people management from the case study
- As a conclusion, write a short reflection on the people management aspect of the case study (transformation project) and also list 2 lessons you have learned from this case study that may help you manage people more effectively in your career.
References (list the at least 5 references along with their in-text citations)
Solution
Introduction
The paper focusses on Menlo, WorldWide Logistics' lean warehousing initiative. Utilizing lean warehouse solutions, Menlo was able to provide efficient and lean warehousing services to the customer. In order to reach its goals and objectives, the company relies on an unparalleled group of people. An in-depth analysis evaluating Menlo's project management process was conducted as part of this case study (Bartholomew, 2008). For Assignment help The case study went on to detail the procedures required in improving their processes and, as a result, its general performance as well as income. Such lean waste principles also included some strategies for eliminating waste. Customers' voice and essential customer requirements were also analysed for their impact on process and quality in a study published this week.
Concepts of Lean Framework
The voice of customer
In the given case study the customer for Menlo were the the excavator manufacturer, the tech firm of silicon valley as well as Lam Research which manufacturers semi-conductors. The voice here mainly refers to the desires of the customer, in the current case study the Menlo wanted the following things:
- Boost the accuracy of inventory
- Pickups that are less susceptible to errors should be avoided.
- Streamline operations and reduce transportation and logistics costs
- Increasing output
- Accidents on the job are decreasing at a rate of one per year.
- Achieve annual savings in inventory storage
Quality, safety, delivery, services, and pricing are just few of the ways in which the company measures client satisfaction. This is where Menlo's lean endeavour truly begins: on the production floor of its customer. Using feedback from workers on the final product assembly process, Menlo experts then create the most efficient material flow first from factory through the warehouse towards the ultimate consumer. There were some ground rules put in place by the project team in order to keep the project on track, and so the project team were able to see and hear from the client.
Critical Customer Requirements
In order to have a clear picture of the needs of their customers before beginning a project, businesses utilize Critical Customer Requirement (CCR). As a result, they were able to better grasp their consumers' demands and expectations. Menlo Worldwide Logistics understands that a one-size-fits-all strategy does not operate in most of its warehouses. They adopt a section on the floor according to the lean philosophy. A customer's factory floor is where Menlo's lean endeavour begins. For warehousing tasks like that as picking, packaging, labelling, and shipping, Menlo personnel begin with feedback from final product production line operators and afterwards design the most efficient material flows (Jaisankar & Subbramani, 2016).
Critical to Quality
In order to ensure the efficacy of CSR, Critical to Quality (CTQ) needs to be undertaken at the same time. In order to maintain a high standard of quality, these are tasks that must be carried out in a certain manner. For each customer, Menlo team does a detailed investigation to determine the best material flow from the factory through the warehouse to the final customer. Employees at Menlo are given a lot of attention to ensure the company's high standards are met. For example, every facility management is supposed to not only comprehend the ideas of lean, but to also implement lean techniques on the floor. So, in order to do this, each Menlo facility is required to design and abide to a "30-30 Form," meaning "continual improvement plan." Also every warehouse has devised a monthly 'diet' involving lean tasks which its employees have agreed to follow, and also the outcomes are documented. Lean success is measured in terms of completed projects while also upcoming plans to execute further lean initiatives in each warehouse on a monthly basis (Swarnakar & Vinodh, 2016). Using these procedures, Menlo ensures that it considers the "critical to quality" notion extremely seriously .
Critical to Process
As a massive undertaking, Menlo required warehouse lean implementation to be finished on schedule, therefore the project management team meticulously scheduled every detail. To make sure the project plan remained unchanged during its lifespan, every step of the way was meticulously scrutinised. Adjusting machine temperature, recalibrating machines, and inspecting machines are among the requirements for such process to work well. Another way they meet Critical to Process principle is using Kaizen. Value Stream Mapping and 5S are two methods used by Japanese companies to adopt Kaizen in their operations. Waste will be eliminated in the different warehouse operations and activities as part of a kaizen burst, which will take place within the next 6 months (Dasig, 2017).
Lean Reduction
The 4 of the 8 wastes of lean that apply to Menlo’s operation include Transportation, Waiting, Motion and Inventory (Gladysz et al., 2020).
How was the waste reduced
Transportation
To better serve the heavy-equipment manufacturer, Menlo has created a new production support facility nearby. As a result, the amount of time spent travelling to and from the repair site was significantly decreased. The PMBOK's methodologies are being used to help with this eliminating waste pertained to optimizing project cost management, project time management, including project human resource management (Gladysz et al., 2020).
Waiting
A customer's factory floor is where Menlo's lean endeavour begins. Using feedback from workers here on finished piece assembly line, Menlo personnel then create the most efficient material flow from the factory through the warehouses to the final consumer. As a result of this, the logistics company generates a warehouse plan that emphasises safety and reliability, as well as efficient material flow across warehouse tasks such as sorting, positioning of items and packaging. The project's time management has been the driving force from the beginning. To avoid squandering time, each potential source of it was examined, and a plan devised to address each one.
Motion
The concept of motion is implied in the given case and it is evident by a few instances. First being that the supervisor at Menlo supervised a seven-person team of employees in an on-site clean environment to assess the selection, packaging, transferring, and unpacking process of supplies for a customer that makes semiconductor production equipment. After adding up the hours it took to accomplish every step, this same team came up with a final time of 25.86 minutes. The team analysed the process, seeking for methods to minimise the amount of time it required to complete the different processes. The team was able to speed up the selection process by leveraging lot size and basically integrating two separate processes. The de-trashing of non-sensitive content at the pickup site reduced the procedure to 4.94 mins by removing the cardboard packaging and unpacking of items.
Inventory
The inventory optimization process carried out by Menlo help achieved the lean waste reduction. In order to manufacture services and goods with a Just-in-Time approach, there must be no inventory wastage and Menlp helped achieved the same with their customers. Erroneous forecasting methods, inefficient procedures or vendors, long changeover periods, imbalanced manufacturing processes, or inadequate inventory management and tracking are some of the key tenets which Menlo implemented for their customers.
Impact of Lean Waste Principles on Overall Projects
Lean management concepts have a significant impact on the project's overall efficiency. Personnel and material transfer costs and times are minimised when transportation wastage is decreased. Additionally, the Menlo project was able to save money and time by reducing superfluous operations. It was possible to save money on superfluous items and equipment by eliminating inventory waste. Using a just-in-time strategy, excessive inventory costs are avoided by utilising these resources just when they are needed. Finally, relevant resources, including such equipment and human assets, have been placed in the right places to reduce motion waste. Using Menlo's support, the manufacturing business was able to increase inventory accuracy from 60% to 99.9%; cut value of the inventory by 26%; minimise parts unavailability to 90%; and reduce 95 % of their expedited freight expenditures within the first 5 months of implementation.
Menlo’s lean facility at Fremont, CA achieved the following implementing lean waste principles:
Figure 1 - (Bartholomew, 2008)
In addition to the above, the same Fremont, CA facility reduced the factory to the floor process from 25.86 minutes to just under 5 minutes. This resulted in savings of 44,000 USD.
Tools and techniques from PMBOK
When it comes to project management, process analysis is mostly about adhering to the process transformation program. It's a tool for spotting potential flaws in a project's current blueprint. Because of these issues and many other non-value-added activities, Menlo explored in to the ways to improve their business, including better staff training, a more streamlined method for handling specialised products, and a better grasp on the floor requirements at the factory (GONÇALVES et al., 2017). Another strategy that was employed the most frequently throughout the project was Brainstorming. Having brainstorming sessions on a regular basis allowed the project team to save costs and time. Using these two strategies in tandem was a great aid to the entire project.
Application of 3 principles on the case study
Kaizen
Warehousing Kaizen events are similar to manufacturing Kaizen events, although the work procedures on which they are centered tends to be distinct in the warehousing. A better continual improvement event in the warehousing may be to move a banding machine towards a better place for that operation instead of figuring out how to boost the effectiveness of materials flow towards a welding station. Warehouse tasks such as selecting, outfitting, staging, as well as the actual packing, trucking, and sequencing for delivery will be redesigned in order to improve the flow of supplies. For instance, Employees from Menlo's warehouse collaborated with a high-tech client to construct a set of steel racks to safeguard the client's computer servers during transit between its production facility and its warehouse. During a Kaizen event, individuals who execute the task are involved, while a supervisor or manager acts as a facilitator (Majerus, 2017). It is the goal of each team to examine the process step-by-step and identify any further areas for streamlining by reducing the need for manual labour, material transportation, and other inefficiencies.
5S
For every lean organization to survive, the Five S policy is vital, with the exception that Menlo replaces "sweep" with "shine." Menlo's Fremont warehouse not only has pristine flooring and work areas, but employees are continuously on the alert for any missing products or other garbage. Each kaizen group must undertake a monthly Five S criterion review as a matter of principle. This further strengthens Kaizen in their organization.
Value Stream Mapping
Value-stream mapping is used by Menlo to discover unnecessary steps. As a result of value-stream analysis, Menlo is able to trace the movement of data and items through a facility, subsequently disassemble the process and restructure its components for improved efficiency and effectiveness (Jocson, 2021). After performing a value-stream review and brainstorming to identify areas for improvement and procedures with the most potential for reduction, Menlo personnel would start with a typical warehouse which has not yet attempted lean (Sharma, 2017). In addition, a special team known as the "red tag" is assigned to each site. The role of this red team is to decide simply one thing, eliminate any thing which isn’t needed. This is followed by a Value Stream Map based kaizen roadmap for 6 months.
Conclusion
Human resources are the fundamental means through which a project's hard graft and creativity may be made more effective. Organizational hierarchies have been lowered and their contributions have been recognised in order to improve human resource management efficiency. There was a strong emphasis on employees becoming mentors / subordinates, as well as a strong emphasis on people providing their own feedback. The knowledge gained from this project will be invaluable in the future when it comes to mitigating project risks and ensuring that the correct people are assigned to the proper jobs. A project's ability to learn and grow depends on its ability to assemble a strong team. The next time I have a team project, I'll remember to put together a well-trained team that could assist me finish it quickly. Another key lesson acquired from this project is the importance of precise planning. This will be useful in the planning of future initiatives. This is not to mention that I gained valuable insights in terms of the practicality of Value Stream Mapping and the incremental improvements via Kaizen. When I am stuck in a project, I would try to apply the same thought as in to redesign, re-think my way and implement incremental improvements to wade my way through the project.
References
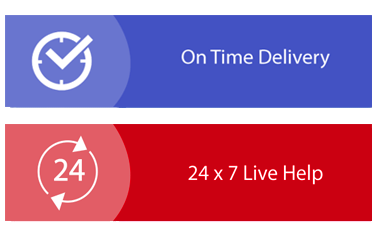
Download Samples PDF
Related Sample
- Internet Use and Economic Development Evidence and Policy Implications Assignment
- Strategic Management Assignment
- LAWS20058 Australian Commercial Law Assignment
- LML6003 Migration Law Assignment
- CSM80017 Managing Quality and Safety in Construction Site Operation Assignment
- MIS102 Data and Networking Assignment
- PROJ6004 Contracts and Procurement
- COIT20250 Emerging Technologies in E business Assignment
- MIS101 Information Systems for Business Assignment
- MBA622 Comprehensive Healthcare Strategies Report
- BAS121 A Fundamentals of Marketing Assignment
- PRJ5106 Research Methodology and Data Analysis Report 1
- BUS2004 Human Resource Management Assignment
- PBHL20009 Assessment Sample
- PUBH6206 Health Promotion and Community Health Assignment
- Masters Degree Dissertation Assignment
- MBA Capstone Strategy Assessment
- ISYS6008 IT Entrepreneurship And Innovation Assignment
- MIS300 Systems Analysis and Design
- MBA652 Strategy and Leadership in Tourism and Hospitality Report 1
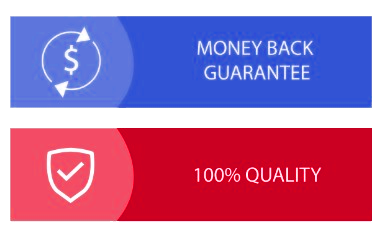
Assignment Services
-
Assignment Writing
-
Academic Writing Services
- HND Assignment Help
- SPSS Assignment Help
- College Assignment Help
- Writing Assignment for University
- Urgent Assignment Help
- Architecture Assignment Help
- Total Assignment Help
- All Assignment Help
- My Assignment Help
- Student Assignment Help
- Instant Assignment Help
- Cheap Assignment Help
- Global Assignment Help
- Write My Assignment
- Do My Assignment
- Solve My Assignment
- Make My Assignment
- Pay for Assignment Help
-
Management
- Management Assignment Help
- Business Management Assignment Help
- Financial Management Assignment Help
- Project Management Assignment Help
- Supply Chain Management Assignment Help
- Operations Management Assignment Help
- Risk Management Assignment Help
- Strategic Management Assignment Help
- Logistics Management Assignment Help
- Global Business Strategy Assignment Help
- Consumer Behavior Assignment Help
- MBA Assignment Help
- Portfolio Management Assignment Help
- Change Management Assignment Help
- Hospitality Management Assignment Help
- Healthcare Management Assignment Help
- Investment Management Assignment Help
- Market Analysis Assignment Help
- Corporate Strategy Assignment Help
- Conflict Management Assignment Help
- Marketing Management Assignment Help
- Strategic Marketing Assignment Help
- CRM Assignment Help
- Marketing Research Assignment Help
- Human Resource Assignment Help
- Business Assignment Help
- Business Development Assignment Help
- Business Statistics Assignment Help
- Business Ethics Assignment Help
- 4p of Marketing Assignment Help
- Pricing Strategy Assignment Help
- Nursing
-
Finance
- Finance Assignment Help
- Do My Finance Assignment For Me
- Financial Accounting Assignment Help
- Behavioral Finance Assignment Help
- Finance Planning Assignment Help
- Personal Finance Assignment Help
- Financial Services Assignment Help
- Forex Assignment Help
- Financial Statement Analysis Assignment Help
- Capital Budgeting Assignment Help
- Financial Reporting Assignment Help
- International Finance Assignment Help
- Business Finance Assignment Help
- Corporate Finance Assignment Help
-
Accounting
- Accounting Assignment Help
- Managerial Accounting Assignment Help
- Taxation Accounting Assignment Help
- Perdisco Assignment Help
- Solve My Accounting Paper
- Business Accounting Assignment Help
- Cost Accounting Assignment Help
- Taxation Assignment Help
- Activity Based Accounting Assignment Help
- Tax Accounting Assignment Help
- Financial Accounting Theory Assignment Help
-
Computer Science and IT
- Operating System Assignment Help
- Data mining Assignment Help
- Robotics Assignment Help
- Computer Network Assignment Help
- Database Assignment Help
- IT Management Assignment Help
- Network Topology Assignment Help
- Data Structure Assignment Help
- Business Intelligence Assignment Help
- Data Flow Diagram Assignment Help
- UML Diagram Assignment Help
- R Studio Assignment Help
-
Law
- Law Assignment Help
- Business Law Assignment Help
- Contract Law Assignment Help
- Tort Law Assignment Help
- Social Media Law Assignment Help
- Criminal Law Assignment Help
- Employment Law Assignment Help
- Taxation Law Assignment Help
- Commercial Law Assignment Help
- Constitutional Law Assignment Help
- Corporate Governance Law Assignment Help
- Environmental Law Assignment Help
- Criminology Assignment Help
- Company Law Assignment Help
- Human Rights Law Assignment Help
- Evidence Law Assignment Help
- Administrative Law Assignment Help
- Enterprise Law Assignment Help
- Migration Law Assignment Help
- Communication Law Assignment Help
- Law and Ethics Assignment Help
- Consumer Law Assignment Help
- Science
- Biology
- Engineering
-
Humanities
- Humanities Assignment Help
- Sociology Assignment Help
- Philosophy Assignment Help
- English Assignment Help
- Geography Assignment Help
- Agroecology Assignment Help
- Psychology Assignment Help
- Social Science Assignment Help
- Public Relations Assignment Help
- Political Science Assignment Help
- Mass Communication Assignment Help
- History Assignment Help
- Cookery Assignment Help
- Auditing
- Mathematics
-
Economics
- Economics Assignment Help
- Managerial Economics Assignment Help
- Econometrics Assignment Help
- Microeconomics Assignment Help
- Business Economics Assignment Help
- Marketing Plan Assignment Help
- Demand Supply Assignment Help
- Comparative Analysis Assignment Help
- Health Economics Assignment Help
- Macroeconomics Assignment Help
- Political Economics Assignment Help
- International Economics Assignments Help
-
Academic Writing Services
-
Essay Writing
- Essay Help
- Essay Writing Help
- Essay Help Online
- Online Custom Essay Help
- Descriptive Essay Help
- Help With MBA Essays
- Essay Writing Service
- Essay Writer For Australia
- Essay Outline Help
- illustration Essay Help
- Response Essay Writing Help
- Professional Essay Writers
- Custom Essay Help
- English Essay Writing Help
- Essay Homework Help
- Literature Essay Help
- Scholarship Essay Help
- Research Essay Help
- History Essay Help
- MBA Essay Help
- Plagiarism Free Essays
- Writing Essay Papers
- Write My Essay Help
- Need Help Writing Essay
- Help Writing Scholarship Essay
- Help Writing a Narrative Essay
- Best Essay Writing Service Canada
-
Dissertation
- Biology Dissertation Help
- Academic Dissertation Help
- Nursing Dissertation Help
- Dissertation Help Online
- MATLAB Dissertation Help
- Doctoral Dissertation Help
- Geography Dissertation Help
- Architecture Dissertation Help
- Statistics Dissertation Help
- Sociology Dissertation Help
- English Dissertation Help
- Law Dissertation Help
- Dissertation Proofreading Services
- Cheap Dissertation Help
- Dissertation Writing Help
- Marketing Dissertation Help
- Programming
-
Case Study
- Write Case Study For Me
- Business Law Case Study Help
- Civil Law Case Study Help
- Marketing Case Study Help
- Nursing Case Study Help
- Case Study Writing Services
- History Case Study help
- Amazon Case Study Help
- Apple Case Study Help
- Case Study Assignment Help
- ZARA Case Study Assignment Help
- IKEA Case Study Assignment Help
- Zappos Case Study Assignment Help
- Tesla Case Study Assignment Help
- Flipkart Case Study Assignment Help
- Contract Law Case Study Assignments Help
- Business Ethics Case Study Assignment Help
- Nike SWOT Analysis Case Study Assignment Help
- Coursework
- Thesis Writing
- CDR
- Research