Order Now
- Home
- About Us
-
Services
-
Assignment Writing
-
Academic Writing Services
- HND Assignment Help
- SPSS Assignment Help
- College Assignment Help
- Writing Assignment for University
- Urgent Assignment Help
- Architecture Assignment Help
- Total Assignment Help
- All Assignment Help
- My Assignment Help
- Student Assignment Help
- Instant Assignment Help
- Cheap Assignment Help
- Global Assignment Help
- Write My Assignment
- Do My Assignment
- Solve My Assignment
- Make My Assignment
- Pay for Assignment Help
-
Management
- Management Assignment Help
- Business Management Assignment Help
- Financial Management Assignment Help
- Project Management Assignment Help
- Supply Chain Management Assignment Help
- Operations Management Assignment Help
- Risk Management Assignment Help
- Strategic Management Assignment Help
- Logistics Management Assignment Help
- Global Business Strategy Assignment Help
- Consumer Behavior Assignment Help
- MBA Assignment Help
- Portfolio Management Assignment Help
- Change Management Assignment Help
- Hospitality Management Assignment Help
- Healthcare Management Assignment Help
- Investment Management Assignment Help
- Market Analysis Assignment Help
- Corporate Strategy Assignment Help
- Conflict Management Assignment Help
- Marketing Management Assignment Help
- Strategic Marketing Assignment Help
- CRM Assignment Help
- Marketing Research Assignment Help
- Human Resource Assignment Help
- Business Assignment Help
- Business Development Assignment Help
- Business Statistics Assignment Help
- Business Ethics Assignment Help
- 4p of Marketing Assignment Help
- Pricing Strategy Assignment Help
- Nursing
-
Finance
- Finance Assignment Help
- Do My Finance Assignment For Me
- Financial Accounting Assignment Help
- Behavioral Finance Assignment Help
- Finance Planning Assignment Help
- Personal Finance Assignment Help
- Financial Services Assignment Help
- Forex Assignment Help
- Financial Statement Analysis Assignment Help
- Capital Budgeting Assignment Help
- Financial Reporting Assignment Help
- International Finance Assignment Help
- Business Finance Assignment Help
- Corporate Finance Assignment Help
-
Accounting
- Accounting Assignment Help
- Managerial Accounting Assignment Help
- Taxation Accounting Assignment Help
- Perdisco Assignment Help
- Solve My Accounting Paper
- Business Accounting Assignment Help
- Cost Accounting Assignment Help
- Taxation Assignment Help
- Activity Based Accounting Assignment Help
- Tax Accounting Assignment Help
- Financial Accounting Theory Assignment Help
-
Computer Science and IT
- Operating System Assignment Help
- Data mining Assignment Help
- Robotics Assignment Help
- Computer Network Assignment Help
- Database Assignment Help
- IT Management Assignment Help
- Network Topology Assignment Help
- Data Structure Assignment Help
- Business Intelligence Assignment Help
- Data Flow Diagram Assignment Help
- UML Diagram Assignment Help
- R Studio Assignment Help
-
Law
- Law Assignment Help
- Business Law Assignment Help
- Contract Law Assignment Help
- Tort Law Assignment Help
- Social Media Law Assignment Help
- Criminal Law Assignment Help
- Employment Law Assignment Help
- Taxation Law Assignment Help
- Commercial Law Assignment Help
- Constitutional Law Assignment Help
- Corporate Governance Law Assignment Help
- Environmental Law Assignment Help
- Criminology Assignment Help
- Company Law Assignment Help
- Human Rights Law Assignment Help
- Evidence Law Assignment Help
- Administrative Law Assignment Help
- Enterprise Law Assignment Help
- Migration Law Assignment Help
- Communication Law Assignment Help
- Law and Ethics Assignment Help
- Consumer Law Assignment Help
- Science
- Biology
- Engineering
-
Humanities
- Humanities Assignment Help
- Sociology Assignment Help
- Philosophy Assignment Help
- English Assignment Help
- Geography Assignment Help
- Agroecology Assignment Help
- Psychology Assignment Help
- Social Science Assignment Help
- Public Relations Assignment Help
- Political Science Assignment Help
- Mass Communication Assignment Help
- History Assignment Help
- Cookery Assignment Help
- Auditing
- Mathematics
-
Economics
- Economics Assignment Help
- Managerial Economics Assignment Help
- Econometrics Assignment Help
- Microeconomics Assignment Help
- Business Economics Assignment Help
- Marketing Plan Assignment Help
- Demand Supply Assignment Help
- Comparative Analysis Assignment Help
- Health Economics Assignment Help
- Macroeconomics Assignment Help
- Political Economics Assignment Help
- International Economics Assignments Help
-
Academic Writing Services
-
Essay Writing
- Essay Help
- Essay Writing Help
- Essay Help Online
- Online Custom Essay Help
- Descriptive Essay Help
- Help With MBA Essays
- Essay Writing Service
- Essay Writer For Australia
- Essay Outline Help
- illustration Essay Help
- Response Essay Writing Help
- Professional Essay Writers
- Custom Essay Help
- English Essay Writing Help
- Essay Homework Help
- Literature Essay Help
- Scholarship Essay Help
- Research Essay Help
- History Essay Help
- MBA Essay Help
- Plagiarism Free Essays
- Writing Essay Papers
- Write My Essay Help
- Need Help Writing Essay
- Help Writing Scholarship Essay
- Help Writing a Narrative Essay
- Best Essay Writing Service Canada
-
Dissertation
- Biology Dissertation Help
- Academic Dissertation Help
- Nursing Dissertation Help
- Dissertation Help Online
- MATLAB Dissertation Help
- Doctoral Dissertation Help
- Geography Dissertation Help
- Architecture Dissertation Help
- Statistics Dissertation Help
- Sociology Dissertation Help
- English Dissertation Help
- Law Dissertation Help
- Dissertation Proofreading Services
- Cheap Dissertation Help
- Dissertation Writing Help
- Marketing Dissertation Help
- Programming
-
Case Study
- Write Case Study For Me
- Business Law Case Study Help
- Civil Law Case Study Help
- Marketing Case Study Help
- Nursing Case Study Help
- Case Study Writing Services
- History Case Study help
- Amazon Case Study Help
- Apple Case Study Help
- Case Study Assignment Help
- ZARA Case Study Assignment Help
- IKEA Case Study Assignment Help
- Zappos Case Study Assignment Help
- Tesla Case Study Assignment Help
- Flipkart Case Study Assignment Help
- Contract Law Case Study Assignments Help
- Business Ethics Case Study Assignment Help
- Nike SWOT Analysis Case Study Assignment Help
- Coursework
- Thesis Writing
- CDR
- Research
-
Assignment Writing
-
Resources
- Referencing Guidelines
-
Universities
-
Australia
- Asia Pacific International College Assignment Help
- Macquarie University Assignment Help
- Rhodes College Assignment Help
- APIC University Assignment Help
- Torrens University Assignment Help
- Kaplan University Assignment Help
- Holmes University Assignment Help
- Griffith University Assignment Help
- VIT University Assignment Help
- CQ University Assignment Help
-
Australia
- Experts
- Free Sample
- Testimonial
EAT80002 Professional Master's Industry Project Report Sample
INTRODUCTION
In this assessment, you are required to prepare a proposal and plan for your allocated industry-linked project. This follows discussions held with your industry and academic supervisors, and your preliminary review of relevant literature. It is expected that you have clarified the problem worth solving to the industry partner and identified an approach or solution that you intend to explore in more depth in the remainder of the semester. This assessment aims to help you develop a value proposition and determine the specific stages and activities that you need to achieve in this project, including the design, research or development work that is required.
DESCRIPTION Your submission should be a document written in the form of a tender or grant proposal that makes the case for the proposed project based on an initial preliminary investigation. It should include statements on:
- The main problem and key questions to address: this should have adequate background information from industry and literature to show that the problem is worth solving to the industry partner and has some validity (it is not simply a whim of the students or supervisors)
- The value, aim and objectives of the project
- The methodological perspectives that underpin your development of the project proposal/plan, including any theory, data required, etc.
- An outline of the methods that you will use to answer the key questions (e.g., experiments, simulations, theoretical modelling, surveys, etc.).
- A plan for the conduct of the project: this should provide a high-level overview of plans for the entire project including key stages and timelines, and a more detailed overview of specific activities for the semester. These should be consistent with the proposed aim and objectives of the project.
- Required resources, including a description of how these resources will be sourced (e.g. access to labs/workshops, funding for projects, software, materials required if known, etc.).
- A general outline of the division of tasks amongst the group members
REQUIRED LENGTH FOR ASSESSMENT COMPONENTS
1. A written proposal (minimum word-count: 2,000 words, excluding references and cover page), preferably sighted and reviewed by your industry project supervisor
2. An outline of the semester plan drafted according to semester weeks and calendar weeks. A Gantt chart is recommended with written milestones and key deliverables
3. Explanations that fully describe activities related to each milestone
4. An outline of group task allocation, drafted according to key milestones and deliverables
Solution
1. Introduction
Energys Australia, one of the world’s first movers in hydrogen energy technology, is committed to popularizing the use of hydrogen energy, making it affordable and easy to obtain. Currently the company has designed a hydrogen fuel cell for use in only stationery application but plans this to be taken to dynamic uses. For this purpose, they must be able to elicit and analyse the fuel cell’s performance under dynamic loading conditions; issues like the stability of the components, vibration and structural integrity come into play. The goal of this project for The Assignment Helpline is to analyse, evaluate the feasibility, material selection and design of some of the component supports and the vibration protection for the hydrogen fuel cell using Ansys software.
2. Background
Fuel cells particularly those that utilises hydrogen are today decried as a clean technology with the capability of generating electricity from hydrogen and oxygen chemicals with water as the only emission. However, due to the structural sensitivity of many of the components to external forces, the practical use of fuel cells, specifically hydrogen fuel cells, in dynamic surroundings (for example, in mobile objects or in zones with high levels of vibrations) still poses certain problems. In dynamic loading cases, vibrations have influence on functions, reliability and durability of the fuel cell (Hassan et al. 2021).
Figure 1: hydrogen fuel cell generator
(Source: energys.com.au)
Previous research investigated on the vibration analysis conversely the structural support of hydrogen fuel cells which are susceptible to dynamic loads as it is observed in automotive and aerospace manufacturing firms. The key difficulties that can be met in such a project are the following, and this work will focus on the assessment of the current design proposal.
3. Problem Statement
The integrated hydrogen fuel cell system of Energy’s Australia is at the moment not transportable thanks to structural issues regarding its stability and performance under dynamic loads. The need to introduce the fuel cell into a situation where there are varying external forces mean that there is need to undertake a test on part and component supports as well as the vibration protection. Among the technologies, hydrogen fuel cells are promising in renewal energy, especially in stationary uses. Nonetheless, the ability to operate in dynamic environments, for instance in mobile systems or environments affected by vibration is a major challenge (Tang et al. 2021). The currently used hydrogen fuel cell in Energys Australia is fixed in a rigid structure that cannot be moved, and the performance of this fuel cell is likely to be compromised by dynamic loading and or component failure. Dynamic loads which include vibrations, shocks and the likes put mechanical loads on various parts and can cause fatigue, misalignment or even failure of some very vital parts or even an in entire system. In the future when designing vehicles for transportation or portable usage of hydrogen fuel cells, stability and vibration protection will prove to be significant. The failure to meet these challenges might slow down the possibilities of large scale and application of hydrogen fuel cells across various sectors. Hence, this project is very important in detecting, studying, and managing the impacts of dynamic loads on the fuel cell hence guaranteeing its efficiency and durability in different operating conditions.
4. Key Questions
• In what manner do the loading condition changes (vibration, shock) impact the structural design as well as the efficiency of the hydrogen fuel cell?
• What current design constraints are relevant to the numbers and types of components which can be supported and the degree of protection from vibration?
• Which potential design features that ought to be described to overcome these limits are; in what ways can they be adjusted in design or material choice?
• What is the best way to arrange supports and damping mechanisms?
Value: The project opened immense value for Energy’s Australia since they have a hydrogen fuel cell technology accrued employable in dynamic realms. This will extend the usage of their product that makes them to have a new market in transport and other mobile uses.
5. Aim and objectives
Aim
This research project aims at assessing and optimising the component supports and vibration safeguards for the hydrogen fuel cell of Energy’s Australia under dynamic loads.
Objectives
• To perform a comprehensive literature review on hydrogen fuel cells subjected to dynamic loads.
• To model the hydrogen fuel cell in Ansys software and simulate various dynamic loading scenarios.
• To identify critical points of failure or instability in the existing design.
• To propose design modifications to improve component supports and vibration protection.
• To validate the proposed design improvements through further simulations and analysis.
6. Literature Review
The first of these is the collection of background data which is accomplished using a comprehensive literature search. This will encompass researches in areas like the effect of dynamic loads on hydrogen fuel cells; Effects such as vibrations, shocks and any other force which may have an influence on the performance or life cycle of these systems. The review will also look at the current solutions for the protection against vibrations, that is, compositions, pillars as well as the damps. The knowledge from this research will give the framework to reference that can help or hinder, for the further options in the simulation and design aspect of the project.
- Ansys Simulations: Ansys software will be the principal software to analyse the hydrogen fuel cell under different dynamic load conditions. In the actual simulation, there will be significant use of finite element modelling (FEM) to determine stress distribution, deformation and vibration on fuel cell parts. Three specific dynamic load cases will be considered:
1. Harmonic Analysis: This analysis will also determine the effect of sinusoidal loads on the fuel cell since they are some of the most prevalent dynamic loads. Understanding the natural frequencies and resonance characteristic, it will be possible to correlate the fuel cell structural design for vulnerability to destructive vibrations that may cause fatigue or failure.
2. Random Vibration Analysis: This one will simulate environmental conditions as those during transportation or operation in vibrating conditions (Xu et al. 2022). The modal analysis will also include random vibration analysis that will indicate how the various parts of the fuel cell respond to random forces so as to determine the regions that need reinforcement or better damping.
3. Transient Dynamic Analysis: This analysis will assess how the organisation can adjust and respond to changes in the external environment in relation to fuel cell structure. Dynamic analysis of a short duration is important in determining how the fuel cell will behave when exposed to events in which forces are enormous though brief, such as in cases of accidents or sudden motions.
- Design Modification and Optimization: All these results are based on the Ansys simulations; the following step is to offer design changes. This may involve modification of the supports, inclusion of isolators, or the fact that materials used have better damping characteristics. As for each of the modifications proposed, more simulations will have to be made to check their performance. This is an iterative procedure, whereby the design will be modified to suit results elicited from the simulation till the best performance is obtained.
- Validation: However, having developed detailed design changes to the fuel cell design issues investigated in this paper, the improved fuel cell design will go through a validation process. This includes carrying out the final simulations at the dynamic loading conditions in order to check if the enhancements meet the required performance standards. The validation will assure the fuel cell to meet the dynamic loads requirements without exporting structural or efficiency characteristics. If needed, other optimizations will be made to guarantee that the design will be stable and precise under all the pressure expected.
7. Methodological Perspectives
In this project, the theoretical part will be based on the methodological framework that involved model based modelling, simulation and empirical analysis. The four cornerstones of the developing methodology will be drawn and grounded on structural dynamics, vibration analysis and material science.
Key methodologies
- Finite Element Analysis (FEA): Fem Analysis will be carried out using Ansys software where dynamic loading condition will be simulated and the impact of such conditions on the fuel cell components in terms of stress distribution, deformation and vibration will be determined.
- Dynamic Load Analysis: Several dynamic loads will be applied to the fuel cell: harmonic and random vibrations as well as transient dynamic loadings that will mimic operating conditions.
- Material Selection and Analysis: The selection of the materials for components and supports will be according to their way how they can handle dynamic loads with special consideration of damping characteristics and energy absorption.
- Design Optimization: The findings given by the simulations will guide improvement of the designs regarding support structures as well as putting into consideration vibration damper or isolator.
The methods used to address the key questions will include:
- Literature Review: For that purpose, this paragraph aims to provide general information about dynamic loads’ influence on hydrogen fuel cells and the existing approaches to vibration protection.
- Ansys Simulations: The primary assessment tool for the current design and testing change affects. The following dynamic load cases will be considered:
1. Harmonic Analysis: In order to test the nature of the response of the fuel cell to sinusoidal loads.
2. Random Vibration Analysis: For instance, for testing of automobile parts, other parts, or products generally subject to transport, then the environmental conditions to be emulated include the following.
3. Transient Dynamic Analysis: In order to monitor and measure its behaviour in response to sudden forces or shocks.
- Design Modification and Optimization: According to the conclusion of the simulation, suggestions of modification of the design would be made, tried and improved (Qiu et al. 2021).
- Validation: The final design will then be tested for its performance by performing simulations so as to satisfy the measures required under dynamic conditions.
The ways in which the key questions will be addressed will be through theoretical research based on simulations and iterative design. These methods are aimed at assess the overall performance of the hydrogen fuel cell, under dynamic loading condition and recommends and solutions that improves the structure-of-structure and vibration control.
8. Project Plan and Timeline
The project will be conducted over two semesters, with the following stages and timeline
Figure 2: GANT CHART
9. Required Resources
Software: Ansys software for simulated FEA for data analysis.
Hardware: Access to high-performance computing resources to run complex simulations.
Materials: Specifications of the hydrogen fuel cell components provided by Energy’s Australia.
Lab/Workshop Access: Potential access to vibration testing equipment, if required for experimental validation.
Funding: The project may require funding for software licenses, hardware resources, and material testing, to be coordinated with the university and industry partner.
However, to achieve this and be able to implement this project, there is need to acquire a lot of software and hardware support. The Ansys software will be used as the primary Software for simulation and the Finite element analysis of the hydrogen fuel cell and to analyse the models describing the dynamic states. The simulation information will be processed and analysed to give a reliable end product (Luo et al. 2021). Department of Grids and High-Performance Computing Resources will be crucial in addressing the computational intensity of the simulations for it to produce good results. Energy’s Australia has been securing the specifications of the hydrogen fuel cell components that will be used in the simulations and design change. Also, other unidentified structures that may be used in a laboratory or workshop for testing some array of vibration testing equipment may also be required for experimental purposes to verify some of the simulation findings. Research funding will come in handy when it comes to expenditure like license fees, appropriate hardware and testing of different kinds of materials. These resources will have to be sourced from the university or from the industrial partner with whom the project will have to be coordinated to ensure its success.
10. Division of Tasks
The project will be divided among the group members as follows:
1. Project Management and Coordination: Coordination of the general status of the project and putting into consideration timely delivery of the project.
2. Literature Review and Background Research: Carrying out a literature and writing a review of the specific literature and current practices in the industry.
3. Modelling and Simulation: Developing a model of the fuel cell in Ansys and going through with the simulations.
4. Design and Optimization: Basic Approaches: Simulation analysis and recommendation of changes to the design.
5. Validation and Reporting: Sharing, reviewing the results, finalising the design, and creating the project report and presentation.
11. Conclusion
The objective of this project is to supply Energy’s Australia with a sound strategy for making their hydrogen fuel cell technology applicable to various settings. The project will improve and develop additional supports for specific components, and other forms of vibration mitigation, to advance the use of hydrogen fuel cells in mobile and transportable applications that build on the benefits of clean energy.
References
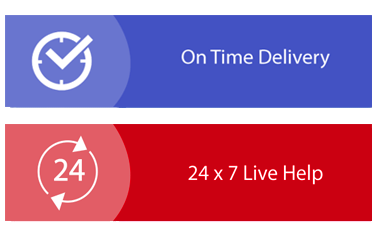
Download Samples PDF
Related Sample
- COIT20263 Information Security Management Report 1
- Model Based Systems Engineering Report Sample
- MCR002B Organisational Behaviour Assignment
- Managing Information Systems Technology Projects
- Leadership and Effecting Change in Public Health Assignment
- FIN2SEV Investment Securities Assignment
- UMH207 Understanding Mental Health Assignment
- MANU2117 Integrated logistic support Management Assignment
- MBAS905 Advanced Business Analytics Case Study 1
- COMP1001 Data Communications and Networks Assignment
- PRJ5105 Project Integration and Change Management Assignment
- ECO500 Economics for Business Assignment
- MGT502 Business Communication Report
- MIS102 Data and Networking Assignment
- Capstone A Applied Research Project in Public Health
- SENG205 Software Engineering Assignment
- MIS101 Information Systems for Business Assignment
- BSBSTR601 Manage Innovation and Continuous Improvement Assignment
- Project Management Workshop Assignment
- Engineering Strategy Assessment
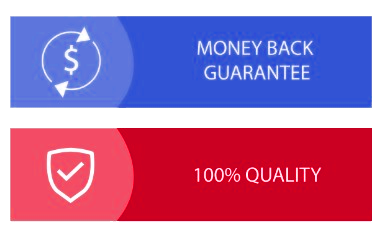
Assignment Services
-
Assignment Writing
-
Academic Writing Services
- HND Assignment Help
- SPSS Assignment Help
- College Assignment Help
- Writing Assignment for University
- Urgent Assignment Help
- Architecture Assignment Help
- Total Assignment Help
- All Assignment Help
- My Assignment Help
- Student Assignment Help
- Instant Assignment Help
- Cheap Assignment Help
- Global Assignment Help
- Write My Assignment
- Do My Assignment
- Solve My Assignment
- Make My Assignment
- Pay for Assignment Help
-
Management
- Management Assignment Help
- Business Management Assignment Help
- Financial Management Assignment Help
- Project Management Assignment Help
- Supply Chain Management Assignment Help
- Operations Management Assignment Help
- Risk Management Assignment Help
- Strategic Management Assignment Help
- Logistics Management Assignment Help
- Global Business Strategy Assignment Help
- Consumer Behavior Assignment Help
- MBA Assignment Help
- Portfolio Management Assignment Help
- Change Management Assignment Help
- Hospitality Management Assignment Help
- Healthcare Management Assignment Help
- Investment Management Assignment Help
- Market Analysis Assignment Help
- Corporate Strategy Assignment Help
- Conflict Management Assignment Help
- Marketing Management Assignment Help
- Strategic Marketing Assignment Help
- CRM Assignment Help
- Marketing Research Assignment Help
- Human Resource Assignment Help
- Business Assignment Help
- Business Development Assignment Help
- Business Statistics Assignment Help
- Business Ethics Assignment Help
- 4p of Marketing Assignment Help
- Pricing Strategy Assignment Help
- Nursing
-
Finance
- Finance Assignment Help
- Do My Finance Assignment For Me
- Financial Accounting Assignment Help
- Behavioral Finance Assignment Help
- Finance Planning Assignment Help
- Personal Finance Assignment Help
- Financial Services Assignment Help
- Forex Assignment Help
- Financial Statement Analysis Assignment Help
- Capital Budgeting Assignment Help
- Financial Reporting Assignment Help
- International Finance Assignment Help
- Business Finance Assignment Help
- Corporate Finance Assignment Help
-
Accounting
- Accounting Assignment Help
- Managerial Accounting Assignment Help
- Taxation Accounting Assignment Help
- Perdisco Assignment Help
- Solve My Accounting Paper
- Business Accounting Assignment Help
- Cost Accounting Assignment Help
- Taxation Assignment Help
- Activity Based Accounting Assignment Help
- Tax Accounting Assignment Help
- Financial Accounting Theory Assignment Help
-
Computer Science and IT
- Operating System Assignment Help
- Data mining Assignment Help
- Robotics Assignment Help
- Computer Network Assignment Help
- Database Assignment Help
- IT Management Assignment Help
- Network Topology Assignment Help
- Data Structure Assignment Help
- Business Intelligence Assignment Help
- Data Flow Diagram Assignment Help
- UML Diagram Assignment Help
- R Studio Assignment Help
-
Law
- Law Assignment Help
- Business Law Assignment Help
- Contract Law Assignment Help
- Tort Law Assignment Help
- Social Media Law Assignment Help
- Criminal Law Assignment Help
- Employment Law Assignment Help
- Taxation Law Assignment Help
- Commercial Law Assignment Help
- Constitutional Law Assignment Help
- Corporate Governance Law Assignment Help
- Environmental Law Assignment Help
- Criminology Assignment Help
- Company Law Assignment Help
- Human Rights Law Assignment Help
- Evidence Law Assignment Help
- Administrative Law Assignment Help
- Enterprise Law Assignment Help
- Migration Law Assignment Help
- Communication Law Assignment Help
- Law and Ethics Assignment Help
- Consumer Law Assignment Help
- Science
- Biology
- Engineering
-
Humanities
- Humanities Assignment Help
- Sociology Assignment Help
- Philosophy Assignment Help
- English Assignment Help
- Geography Assignment Help
- Agroecology Assignment Help
- Psychology Assignment Help
- Social Science Assignment Help
- Public Relations Assignment Help
- Political Science Assignment Help
- Mass Communication Assignment Help
- History Assignment Help
- Cookery Assignment Help
- Auditing
- Mathematics
-
Economics
- Economics Assignment Help
- Managerial Economics Assignment Help
- Econometrics Assignment Help
- Microeconomics Assignment Help
- Business Economics Assignment Help
- Marketing Plan Assignment Help
- Demand Supply Assignment Help
- Comparative Analysis Assignment Help
- Health Economics Assignment Help
- Macroeconomics Assignment Help
- Political Economics Assignment Help
- International Economics Assignments Help
-
Academic Writing Services
-
Essay Writing
- Essay Help
- Essay Writing Help
- Essay Help Online
- Online Custom Essay Help
- Descriptive Essay Help
- Help With MBA Essays
- Essay Writing Service
- Essay Writer For Australia
- Essay Outline Help
- illustration Essay Help
- Response Essay Writing Help
- Professional Essay Writers
- Custom Essay Help
- English Essay Writing Help
- Essay Homework Help
- Literature Essay Help
- Scholarship Essay Help
- Research Essay Help
- History Essay Help
- MBA Essay Help
- Plagiarism Free Essays
- Writing Essay Papers
- Write My Essay Help
- Need Help Writing Essay
- Help Writing Scholarship Essay
- Help Writing a Narrative Essay
- Best Essay Writing Service Canada
-
Dissertation
- Biology Dissertation Help
- Academic Dissertation Help
- Nursing Dissertation Help
- Dissertation Help Online
- MATLAB Dissertation Help
- Doctoral Dissertation Help
- Geography Dissertation Help
- Architecture Dissertation Help
- Statistics Dissertation Help
- Sociology Dissertation Help
- English Dissertation Help
- Law Dissertation Help
- Dissertation Proofreading Services
- Cheap Dissertation Help
- Dissertation Writing Help
- Marketing Dissertation Help
- Programming
-
Case Study
- Write Case Study For Me
- Business Law Case Study Help
- Civil Law Case Study Help
- Marketing Case Study Help
- Nursing Case Study Help
- Case Study Writing Services
- History Case Study help
- Amazon Case Study Help
- Apple Case Study Help
- Case Study Assignment Help
- ZARA Case Study Assignment Help
- IKEA Case Study Assignment Help
- Zappos Case Study Assignment Help
- Tesla Case Study Assignment Help
- Flipkart Case Study Assignment Help
- Contract Law Case Study Assignments Help
- Business Ethics Case Study Assignment Help
- Nike SWOT Analysis Case Study Assignment Help
- Coursework
- Thesis Writing
- CDR
- Research