Order Now
- Home
- About Us
-
Services
-
Assignment Writing
-
Academic Writing Services
- HND Assignment Help
- SPSS Assignment Help
- College Assignment Help
- Writing Assignment for University
- Urgent Assignment Help
- Architecture Assignment Help
- Total Assignment Help
- All Assignment Help
- My Assignment Help
- Student Assignment Help
- Instant Assignment Help
- Cheap Assignment Help
- Global Assignment Help
- Write My Assignment
- Do My Assignment
- Solve My Assignment
- Make My Assignment
- Pay for Assignment Help
-
Management
- Management Assignment Help
- Business Management Assignment Help
- Financial Management Assignment Help
- Project Management Assignment Help
- Supply Chain Management Assignment Help
- Operations Management Assignment Help
- Risk Management Assignment Help
- Strategic Management Assignment Help
- Logistics Management Assignment Help
- Global Business Strategy Assignment Help
- Consumer Behavior Assignment Help
- MBA Assignment Help
- Portfolio Management Assignment Help
- Change Management Assignment Help
- Hospitality Management Assignment Help
- Healthcare Management Assignment Help
- Investment Management Assignment Help
- Market Analysis Assignment Help
- Corporate Strategy Assignment Help
- Conflict Management Assignment Help
- Marketing Management Assignment Help
- Strategic Marketing Assignment Help
- CRM Assignment Help
- Marketing Research Assignment Help
- Human Resource Assignment Help
- Business Assignment Help
- Business Development Assignment Help
- Business Statistics Assignment Help
- Business Ethics Assignment Help
- 4p of Marketing Assignment Help
- Pricing Strategy Assignment Help
- Nursing
-
Finance
- Finance Assignment Help
- Do My Finance Assignment For Me
- Financial Accounting Assignment Help
- Behavioral Finance Assignment Help
- Finance Planning Assignment Help
- Personal Finance Assignment Help
- Financial Services Assignment Help
- Forex Assignment Help
- Financial Statement Analysis Assignment Help
- Capital Budgeting Assignment Help
- Financial Reporting Assignment Help
- International Finance Assignment Help
- Business Finance Assignment Help
- Corporate Finance Assignment Help
-
Accounting
- Accounting Assignment Help
- Managerial Accounting Assignment Help
- Taxation Accounting Assignment Help
- Perdisco Assignment Help
- Solve My Accounting Paper
- Business Accounting Assignment Help
- Cost Accounting Assignment Help
- Taxation Assignment Help
- Activity Based Accounting Assignment Help
- Tax Accounting Assignment Help
- Financial Accounting Theory Assignment Help
-
Computer Science and IT
- Operating System Assignment Help
- Data mining Assignment Help
- Robotics Assignment Help
- Computer Network Assignment Help
- Database Assignment Help
- IT Management Assignment Help
- Network Topology Assignment Help
- Data Structure Assignment Help
- Business Intelligence Assignment Help
- Data Flow Diagram Assignment Help
- UML Diagram Assignment Help
- R Studio Assignment Help
-
Law
- Law Assignment Help
- Business Law Assignment Help
- Contract Law Assignment Help
- Tort Law Assignment Help
- Social Media Law Assignment Help
- Criminal Law Assignment Help
- Employment Law Assignment Help
- Taxation Law Assignment Help
- Commercial Law Assignment Help
- Constitutional Law Assignment Help
- Corporate Governance Law Assignment Help
- Environmental Law Assignment Help
- Criminology Assignment Help
- Company Law Assignment Help
- Human Rights Law Assignment Help
- Evidence Law Assignment Help
- Administrative Law Assignment Help
- Enterprise Law Assignment Help
- Migration Law Assignment Help
- Communication Law Assignment Help
- Law and Ethics Assignment Help
- Consumer Law Assignment Help
- Science
- Biology
- Engineering
-
Humanities
- Humanities Assignment Help
- Sociology Assignment Help
- Philosophy Assignment Help
- English Assignment Help
- Geography Assignment Help
- Agroecology Assignment Help
- Psychology Assignment Help
- Social Science Assignment Help
- Public Relations Assignment Help
- Political Science Assignment Help
- Mass Communication Assignment Help
- History Assignment Help
- Cookery Assignment Help
- Auditing
- Mathematics
-
Economics
- Economics Assignment Help
- Managerial Economics Assignment Help
- Econometrics Assignment Help
- Microeconomics Assignment Help
- Business Economics Assignment Help
- Marketing Plan Assignment Help
- Demand Supply Assignment Help
- Comparative Analysis Assignment Help
- Health Economics Assignment Help
- Macroeconomics Assignment Help
- Political Economics Assignment Help
- International Economics Assignments Help
-
Academic Writing Services
-
Essay Writing
- Essay Help
- Essay Writing Help
- Essay Help Online
- Online Custom Essay Help
- Descriptive Essay Help
- Help With MBA Essays
- Essay Writing Service
- Essay Writer For Australia
- Essay Outline Help
- illustration Essay Help
- Response Essay Writing Help
- Professional Essay Writers
- Custom Essay Help
- English Essay Writing Help
- Essay Homework Help
- Literature Essay Help
- Scholarship Essay Help
- Research Essay Help
- History Essay Help
- MBA Essay Help
- Plagiarism Free Essays
- Writing Essay Papers
- Write My Essay Help
- Need Help Writing Essay
- Help Writing Scholarship Essay
- Help Writing a Narrative Essay
- Best Essay Writing Service Canada
-
Dissertation
- Biology Dissertation Help
- Academic Dissertation Help
- Nursing Dissertation Help
- Dissertation Help Online
- MATLAB Dissertation Help
- Doctoral Dissertation Help
- Geography Dissertation Help
- Architecture Dissertation Help
- Statistics Dissertation Help
- Sociology Dissertation Help
- English Dissertation Help
- Law Dissertation Help
- Dissertation Proofreading Services
- Cheap Dissertation Help
- Dissertation Writing Help
- Marketing Dissertation Help
- Programming
-
Case Study
- Write Case Study For Me
- Business Law Case Study Help
- Civil Law Case Study Help
- Marketing Case Study Help
- Nursing Case Study Help
- Case Study Writing Services
- History Case Study help
- Amazon Case Study Help
- Apple Case Study Help
- Case Study Assignment Help
- ZARA Case Study Assignment Help
- IKEA Case Study Assignment Help
- Zappos Case Study Assignment Help
- Tesla Case Study Assignment Help
- Flipkart Case Study Assignment Help
- Contract Law Case Study Assignments Help
- Business Ethics Case Study Assignment Help
- Nike SWOT Analysis Case Study Assignment Help
- Coursework
- Thesis Writing
- CDR
- Research
-
Assignment Writing
-
Resources
- Referencing Guidelines
-
Universities
-
Australia
- Asia Pacific International College Assignment Help
- Macquarie University Assignment Help
- Rhodes College Assignment Help
- APIC University Assignment Help
- Torrens University Assignment Help
- Kaplan University Assignment Help
- Holmes University Assignment Help
- Griffith University Assignment Help
- VIT University Assignment Help
- CQ University Assignment Help
-
Australia
- Experts
- Free Sample
- Testimonial
MEM602 Engineering Risk Management Case Study 3 Sample
Task Summary
To complete this assessment, you will identify TWO significant process-based risks as prioritised and listed in the Risk Register (Assessment 2). You are to draw upon the data provided in ALL six modules and provide discussion in the form of a Technological Report of 2,500 words (+/- 10%) as to why these risks are significant for the organisation.
Technology Report criteria:
Refer to the Case Study. Take into account ALL of the case’s context;
1. Identify TWO significant process based risks as prioritised and listed in the Risk Register (Assessment 2);
2. Provide discussion as to why they are deemed as significant;
3. Use the following technological risk sequencing and evaluation techniques (A and B) to further this discussion:
A. Adopt a Decision Tree Analysis (DTA) approach and answer the following questions:
i) What is the decision that must be made;
ii) Identify two significant Process-based risks (for Option A and Option B);
iii) Identify two expected scenarios that focus on the risk’s use of controls with each of these options (an opportunity scenario with the use of risk controls and a deviation away from objectives due to use of risk controls) and the likelihood of each scenario;
iv) determine an expected outcome for each of these scenarios
B. Using the same process-based risk or an alternative (as per level of significance and priority identified in the risk register) apply an Event Tree Analysis (ETA) to determine the functioning/not functioning of the risk controls to mitigate this risk’s consequences. Your lecturer/facilitator will be able to assist in formulating your.
Report structure:
1. Executive Summary (what is the purpose and nature of the report);
2. Contents page;
3. Introduction - Background information;
4. Body (as outlined in Technology Report Criteria);
5. Conclusion;
6. Recommendations;
7. List of References;
8. Appendices
Assessment criteria and weighting is as follows (also refer to the assessment rubric).
1. Group presentation of concepts: 20% of this assessment
2. Analytical depth and discussion of technological risks: 35% of this assessment
3. Critical thinking and reflection: 35% of this assessment
4. Communication of ideas /quality of the style and structure of the response: 10% of this assessment.
Types of media used:
All assessment submissions must be in the form of a written report. The report can be supported by the following types of media:
• static imagery;
• Panopto video;
• PowerPoint slides;
• MPV video
Solution
Introduction
Regular inspections are essential to guaranteeing the dependability and durability of our fleet of vehicles in the face of a dynamic operating environment. The background information and importance of Preventive Maintenance Programs (PMPs) in reducing the risks of machine failures are highlighted in the introduction. For Assignment Help, It emphasizes the financial and operational ramifications of ignoring routine inspections, laying the groundwork for the analysis that follows. A fleet of vehicles' overall productivity and efficiency can be negatively impacted by skipping routine inspections, which can also result in expensive repairs and downtime. It may also present a safety risk to motorists and other users of the road if possible problems are not found and fixed quickly. The report explores the results of several analytical techniques used to explore the complexities of the inspection routine risk, including the Pareto chart, decision tree analysis, process mapping, and event tree analysis. The introduction establishes the context for a thorough examination of the ways in which these analyses provide insights and suggestions to strengthen our preventive maintenance strategies.
The first chosen processed based risk to be evaluated from our risk register is the first on the list which is that of inspection routine.
It is deemed worthy of attention because for the following reasons:
a. On-time routine inspection is vital as it puts in check the risk of any negative surprises that might occur in a machine or equipment, in this case, the vehicles. This is highlighted by Al-Refaie & Almowas (2023, p. 51) as the aim of any Preventive Maintenance Program (PMP) is to minimize as much as possible, the cost of repair and equipment downtime. When this is tackled properly, it results in increase in the useful life of these vehicles, as well as enhancing their systems’ availability. On the other hand, failure to prioritize and treat such risk would lead to lost production capacity or reduced product quality.
b. Secondly, Pirbalouti et al. (2023, p. 1) defines major accidental hazards (MAHs) as hazards that can damage human health environment, damage installations, as well as lead to an organization’s reputation loss. Neglecting this risk of late inspection routine could be detrimental as it can possibly lead to MAH(s).
c. Finally, the occurrence of any or both previous two instances could have a detrimental effect on the image of an organization.
In analysing the above risk, we adopt a Decision Tree Analysis (DTA). In doing so, we follow the method as outlined by Ostrom et al., (2012, p. 172). Firstly, we create an accident classification table by allocating classes to the above possible accidents, describing them, and assigning them costs. This is tabulated below:
Next, we create a table for the probability of these accidents occurring as depicted below:
System A
0.1 x $1,000,000 = $100,000
0.75 x $30,000 = $22,500
0.25 x $3,000,000 = $750,000
Total cost = $100,000 + $22,500 + $750,000 = $872,500
System B
0.2 x $1,000,000 = $200,000
0.5 x $30,000 = $15,000
0.3 x $3,000,000 = $900,000
Total cost = $200,000 + $15,000 + $900,000 = $1,115,000
System C
0.2x $1,000,000 = $200,000
0.55 x $30,000 = $16,500
0.25 x $3,000,000 = $750,000
Total cost = $966,500
From the above analysis, it clear that system/policy A is the way to go.
Representing this analysis in a Decision Tree is shown in the figure below:
NOTE: Still ETA is pending for risk 1, my group mate will add.
Apareto chart is pending my group mate will add
Process mapping.
RTS carried out process failure mapping to identify inefficiencies, challenges, and opportunities to improve their PM process. A flow chart was used to streamline the PM activities and create opportunities for in-depth evaluation. Furthermore, a Pareto chart deployed to aid detail the primary concern of the PM process.
Figure 1.0.
RTS PM Process
Note: Flow chart created by the authors.
Figure 2
Failure mapping within the PM process.
Note: Flow chart created by the authors.
RTS PM pareto evaluation.
Pareto chart performed on RTS PM process indicated that the 80% of the PM challenge are from PM ticket issued late, PM ticket not issued, and PM issued to wrong technician. These issues were analyzed using Decision Tree Analysis (DTA) and Event Tree analysis (ETA). To resolve part of the issues identified, RTS needs to implement an automated system that sends reminders to the manager a day before a task is scheduled for completion. Lastly, integrate a feature in the scheduler to incorporate a latest finish time on the job ticket, enabling the scheduler to notify the manager when this deadline is approaching (see recommendation section).
Figure 1.0
RTS PM pareto chart
Note: Nic, (2021). The Pareto Principle (80-20 rule) explained. https://www.paretolabs.com/the-pareto-principle-80-20-rule-explained/
Figure 1.0
Decision Tree Analysis
Option A Path Value
Path Value 80% success rate =6000*(100-80)/100) *12*20) = 6000*(20/100) *12*20= 6000*48 = $288,000.
Path Value 20% success rate = 6000* ((100-20)/100) *12*20) = 6000*(80/100) *12*20 = 6000*192 = $1,152,000.
Option B Path Value
Path Value 90% success rate =6000*(100-90)/100) *12*20) = 6000*(10/100) *12*20= 6000*24 = $144,000.
Path Value 10% success rate = 6000* (100-10)/100) *12*20) = 6000*(90/100) *12*20 = 6000*216 = $1,296,000.
Option A Cost Branch
Cost branch = Total cost + Path Value
Option A1 = 70,000+288,000 = $358,000
Option A2 = 70,000+1,152,000 = $1,222,000
Option B Cost Branch
Option B1 = 20,000+144,000 = $164,000
Option A2 = 70,000+1,296,000 = $1,326,000
Option Cost
Option A.
Option cost = Cost branch*success rate (%) A1 + Cost Branch*success rate (%) A2
Option cost = (358,000*80%) +(1,222,000*20) = $530,800
Option B.
Option cost = Cost branch*success rate (%) B1 + Cost Branch*success rate (%) B2
Option cost = (164,000*90%) +(1,316,000*10) = $279,200
Option C.
Option cost = $1,440,000
From the above computations, Option B ($279,200) is a viable option for RTS to choose based on the DTA outcome.
Maintenance activities are routinely & integral part of the ETA business processes commonly employing a variety of tools such as hand tools, mechanical devices, electronic instruments, lift equipment, and more. However, the utilization of these tools introduces a notable level of risk. Event Tree Analysis (ETA) emerges as a systematic approach to identifying potential accident scenarios and sequences within complex systems. ETA, employing an inductive methodology, meticulously delineates all conceivable outcomes stemming from an accidental (initiating) event. It takes into account the operational status of safety barriers and factors in additional events and considerations. By utilizing ETA, potential vulnerabilities in the design become apparent, allowing for a comprehensive assessment. This assessment facilitates the implementation of appropriate mitigating measures, enhancing overall safety in the maintenance process (Rausand, 2004).
Figure 1,0
Event tree Analysis
Note: Rausand, M. (2004). System reliability theory; event tree analysis.https://www.ntnu.edu/documents/624876/1277590549/chapt03-eta.pdf/6f3e1b19-4824-4812-adc8-9762d2201c22
PM System failed to lodge Hydraulic Lift Crane for maintenance.
One of the risks higher than maintenance is absence of maintenance of equipment or tools. RTS have a high chance of experiencing a disastrous hydraulic lift collapse within the maintenance activities due to negligence and notable knowledge gap within the operators of this high-risk equipment. The initial challenge identified on the ETA is the PM system failure to lodge hydraulic crane for maintenance. This
The practical application of Event Tree Analysis (ETA) for the given scenario involving a Hydraulic Lift Crane. The sequence of events can be analyzed as follows:
Initiating Event: PM System Failure to Lodge Hydraulic Lift Crane for Maintenance.
This event marks the beginning of the analysis. The preventive maintenance (PM) system fails to schedule the required maintenance for the Hydraulic Lift Crane.
Branche 1- Failure of PM System
PM system failure could be attributed to various reasons such as technical glitches, human error in data entry, or system malfunction that could. This problem could possibly be avoided by taking proactive measures in training employees, system auditing and upgrade to avert human error or negligence. These measures could minimize the likelihood of the undesirable event and promote safety and reliability of the equipment.
Branch 2: Crane Not Maintained
PM system failure could possibly lead to neglect of routine PM operations, thereby translating into late or missed maintenance of the equipment. If the crane is not subjected to the necessary maintenance tasks, it could possibly lead either of the two possible outcomes- triggers the maintenance caution system to signal overdue maintenance schedule or failed caution signal.
Branch 2.1: Warning Not Activated
There's high level safety concern in the event of this failure mode. One critical aspect is the activation of warning systems to alert the maintenance team. If the mechanism that generates alerts regarding the crane's maintenance state fails, the safety precautions are further compromised, leading to a more dangerous situation.
Branch 2.2: Safety Lock Failed
In the absence of maintenance, the failure of a safety lock could be a critical failure point. Safety locks are crucial mechanisms to prevent accidents during crane operations. It is the last line of defense before final breakdown of the equipment. At this point, the outcome is often undesirable and very expensive.
Outcome: Crane Collapsed
The culmination of these events could result in the catastrophic failure of the machinery. In the event collapse occurs, it could possibly result in additional damage to the equipment, the environment, and the potential loss of life of personnel(s) caught up in the case of this disaster.
In practical terms, this Event Tree Analysis helps identify failure mode and their potential consequences. It allows for a systematic evaluation of the factors contributing to the functional failure. This analysis becomes evident that the breakdown in the PM system, lack of maintenance, and failures in warning systems and safety locks are all critical elements that, when combined, lead to the ultimate failure of the crane. Implementing ETA in this scenario enables proactive identification of weaknesses in the maintenance and safety systems, providing an opportunity to address these issues before they escalate into a major incident like a crane collapse (Hulett, 2006).
Recommendation
i. Implement robust preventive maintenance Program (PMP) that prioritizes timely routine inspection to minimize repair cost, reduce equipment downtime, and extend useful life of equipment.
ii. Adapt system A to ensure highest degree of safety, and probability of major accidental hazards (MAHs)
iii. Implement regular system audit, system upgrade, and employee training to minimize human error.
iv. Regularly assess the risk management strategies and make necessary changes to align with business objectives.
v. Adopt comprehensive reporting and documentation system for all maintenance activities.
Conclusion
In conclusion, the analysis of the routine inspection risk highlights how crucial it is to take proactive preventive action. The Decision Tree Analysis directs us toward a system or policy that maximizes overall safety while simultaneously reducing expenses. Our PM process's main obstacles are highlighted by the Pareto chart, which directs us toward focused enhancements. We can efficiently allocate resources and prioritize our efforts to address the most critical issues in our preventive maintenance process by combining the insights from the Pareto chart and Decision Tree Analysis. This all-encompassing strategy makes sure that we are minimizing possible risks in addition to cutting expenses, which eventually results in a safer and more effective operation. While event tree analysis reveals the potentially disastrous effects of a PM system failure and motivates us to give system audits and employee training top priority, process mapping reveals inefficiencies. The recommendation section highlights the need to strengthen our defenses against the risks identified as we navigate these revelations by implementing a strong preventive maintenance program, upgrading our systems, and providing training to our employees. This report acts as a compass, pointing the way toward a proactive and robust approach to risk management and maintenance within our operational environment.
Reference
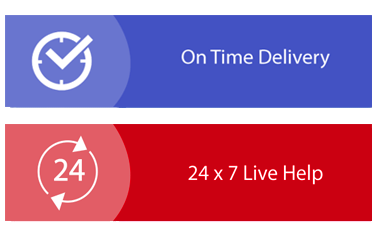
Download Samples PDF
Related Sample
- ICT80008 Professional Issues in IT Assignment
- BUGEN5930 Business Society and The Planet Assignment
- MITS4002 Object Oriented Software Development Assignment
- BSBITU404 Produce Complex Desktop Published Document Assignment
- SHS7000 Food Safety in Association with Campylobacter in Chicken Report
- ACCT6007 Financial Accounting Theory and Practice Research Report
- HI5017 Managerial Accounting Assignment
- BEC4008 Business Economics Assignment
- MME501 Materials of Engineers Report 3
- Cyberwar and International Law Assignment
- MBA5008 Business Research Methods Report 3
- SIT763 Cyber Security Management Assignment
- COIT11226 System Analysis Assignment
- BST903 Financial and Business Analytics Assignment
- MA611 Auditing Assignment
- HI6026 Audit Assurance and Compliance Assignment
- CAM528 Introduction To Epidemiology Assignment
- NRSG367 Transition to Professional Nursing Assignment
- DATA6000 Industry Research Report 4
- IND301A Industry Consulting Project Assignment
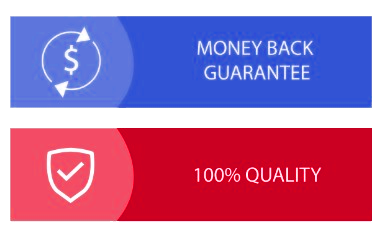
Assignment Services
-
Assignment Writing
-
Academic Writing Services
- HND Assignment Help
- SPSS Assignment Help
- College Assignment Help
- Writing Assignment for University
- Urgent Assignment Help
- Architecture Assignment Help
- Total Assignment Help
- All Assignment Help
- My Assignment Help
- Student Assignment Help
- Instant Assignment Help
- Cheap Assignment Help
- Global Assignment Help
- Write My Assignment
- Do My Assignment
- Solve My Assignment
- Make My Assignment
- Pay for Assignment Help
-
Management
- Management Assignment Help
- Business Management Assignment Help
- Financial Management Assignment Help
- Project Management Assignment Help
- Supply Chain Management Assignment Help
- Operations Management Assignment Help
- Risk Management Assignment Help
- Strategic Management Assignment Help
- Logistics Management Assignment Help
- Global Business Strategy Assignment Help
- Consumer Behavior Assignment Help
- MBA Assignment Help
- Portfolio Management Assignment Help
- Change Management Assignment Help
- Hospitality Management Assignment Help
- Healthcare Management Assignment Help
- Investment Management Assignment Help
- Market Analysis Assignment Help
- Corporate Strategy Assignment Help
- Conflict Management Assignment Help
- Marketing Management Assignment Help
- Strategic Marketing Assignment Help
- CRM Assignment Help
- Marketing Research Assignment Help
- Human Resource Assignment Help
- Business Assignment Help
- Business Development Assignment Help
- Business Statistics Assignment Help
- Business Ethics Assignment Help
- 4p of Marketing Assignment Help
- Pricing Strategy Assignment Help
- Nursing
-
Finance
- Finance Assignment Help
- Do My Finance Assignment For Me
- Financial Accounting Assignment Help
- Behavioral Finance Assignment Help
- Finance Planning Assignment Help
- Personal Finance Assignment Help
- Financial Services Assignment Help
- Forex Assignment Help
- Financial Statement Analysis Assignment Help
- Capital Budgeting Assignment Help
- Financial Reporting Assignment Help
- International Finance Assignment Help
- Business Finance Assignment Help
- Corporate Finance Assignment Help
-
Accounting
- Accounting Assignment Help
- Managerial Accounting Assignment Help
- Taxation Accounting Assignment Help
- Perdisco Assignment Help
- Solve My Accounting Paper
- Business Accounting Assignment Help
- Cost Accounting Assignment Help
- Taxation Assignment Help
- Activity Based Accounting Assignment Help
- Tax Accounting Assignment Help
- Financial Accounting Theory Assignment Help
-
Computer Science and IT
- Operating System Assignment Help
- Data mining Assignment Help
- Robotics Assignment Help
- Computer Network Assignment Help
- Database Assignment Help
- IT Management Assignment Help
- Network Topology Assignment Help
- Data Structure Assignment Help
- Business Intelligence Assignment Help
- Data Flow Diagram Assignment Help
- UML Diagram Assignment Help
- R Studio Assignment Help
-
Law
- Law Assignment Help
- Business Law Assignment Help
- Contract Law Assignment Help
- Tort Law Assignment Help
- Social Media Law Assignment Help
- Criminal Law Assignment Help
- Employment Law Assignment Help
- Taxation Law Assignment Help
- Commercial Law Assignment Help
- Constitutional Law Assignment Help
- Corporate Governance Law Assignment Help
- Environmental Law Assignment Help
- Criminology Assignment Help
- Company Law Assignment Help
- Human Rights Law Assignment Help
- Evidence Law Assignment Help
- Administrative Law Assignment Help
- Enterprise Law Assignment Help
- Migration Law Assignment Help
- Communication Law Assignment Help
- Law and Ethics Assignment Help
- Consumer Law Assignment Help
- Science
- Biology
- Engineering
-
Humanities
- Humanities Assignment Help
- Sociology Assignment Help
- Philosophy Assignment Help
- English Assignment Help
- Geography Assignment Help
- Agroecology Assignment Help
- Psychology Assignment Help
- Social Science Assignment Help
- Public Relations Assignment Help
- Political Science Assignment Help
- Mass Communication Assignment Help
- History Assignment Help
- Cookery Assignment Help
- Auditing
- Mathematics
-
Economics
- Economics Assignment Help
- Managerial Economics Assignment Help
- Econometrics Assignment Help
- Microeconomics Assignment Help
- Business Economics Assignment Help
- Marketing Plan Assignment Help
- Demand Supply Assignment Help
- Comparative Analysis Assignment Help
- Health Economics Assignment Help
- Macroeconomics Assignment Help
- Political Economics Assignment Help
- International Economics Assignments Help
-
Academic Writing Services
-
Essay Writing
- Essay Help
- Essay Writing Help
- Essay Help Online
- Online Custom Essay Help
- Descriptive Essay Help
- Help With MBA Essays
- Essay Writing Service
- Essay Writer For Australia
- Essay Outline Help
- illustration Essay Help
- Response Essay Writing Help
- Professional Essay Writers
- Custom Essay Help
- English Essay Writing Help
- Essay Homework Help
- Literature Essay Help
- Scholarship Essay Help
- Research Essay Help
- History Essay Help
- MBA Essay Help
- Plagiarism Free Essays
- Writing Essay Papers
- Write My Essay Help
- Need Help Writing Essay
- Help Writing Scholarship Essay
- Help Writing a Narrative Essay
- Best Essay Writing Service Canada
-
Dissertation
- Biology Dissertation Help
- Academic Dissertation Help
- Nursing Dissertation Help
- Dissertation Help Online
- MATLAB Dissertation Help
- Doctoral Dissertation Help
- Geography Dissertation Help
- Architecture Dissertation Help
- Statistics Dissertation Help
- Sociology Dissertation Help
- English Dissertation Help
- Law Dissertation Help
- Dissertation Proofreading Services
- Cheap Dissertation Help
- Dissertation Writing Help
- Marketing Dissertation Help
- Programming
-
Case Study
- Write Case Study For Me
- Business Law Case Study Help
- Civil Law Case Study Help
- Marketing Case Study Help
- Nursing Case Study Help
- Case Study Writing Services
- History Case Study help
- Amazon Case Study Help
- Apple Case Study Help
- Case Study Assignment Help
- ZARA Case Study Assignment Help
- IKEA Case Study Assignment Help
- Zappos Case Study Assignment Help
- Tesla Case Study Assignment Help
- Flipkart Case Study Assignment Help
- Contract Law Case Study Assignments Help
- Business Ethics Case Study Assignment Help
- Nike SWOT Analysis Case Study Assignment Help
- Coursework
- Thesis Writing
- CDR
- Research